利用爆炸焊接+热轧工艺制备钛-钢复合板的生产工艺较为成熟,制备的复合板兼具钛材的高比强度、
优良的耐蚀性及钢材的高强度、良好的塑性和易焊性,成本低,生产效率高,产品生命周期长,已成为现代
工业不可缺少的结构材料,广泛应用于石油、化工、船舶和电力等行业[1-3]。
钛-钢爆炸焊接具有一定难度和特殊性,为获得大面积钛-钢复合板,通常采用爆炸焊接+热轧工艺。
钛-钢复合板的结合质量是保证工程结构能够安全服役的关键,原料和生产过程控制不当,将显著降低钛-
钢复合板的结合强度。本研究以爆炸焊接+热轧工艺制备的钛-钢复合板为研究对象,分析由于钛板表面质
量造成的复合界面缺陷,进而优化生产工艺,保证钛-钢复合板的性能满足相关要求。
1、试验材料与方法
采用爆炸焊接+热轧工艺生产钛-钢复合板,复层和基体分别为6mm TA1钛板和30mm Q235B钢板,其性能
见表1。采用线切割截取试样,测试钛-钢复合板性能:拉伸和剪切试验分别按照GB/T 228.1—2010《金属材
料拉伸试验第1部分:室温拉伸方法》和GB/T 6396-2008《复合钢板力学及工艺性能试验方法》进行测试;使
用OLYMPUSGX71金相显微镜进行金相分析,采用Hanemann显微硬度计进行硬度测试,采用氢氟酸(5ml)+硝酸
(12ml)+水(83ml)溶液进行钛组织蚀刻。
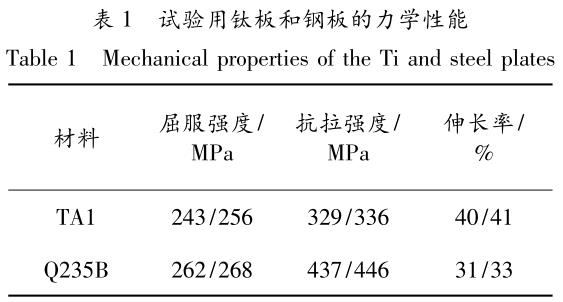
2、结果与讨论
2.1复合板力学性能对比
复合板的理论抗拉强度为Rm=(t1·Rm1+t2·Rm2)/(t1+t2) (1)
其中,Rm为复合板强度下限标准值,Rm1和t1是基材强度下限标准值和厚度,Rm2和t2是复材强度下限标
准值和厚度。
经超声波探伤,复合板内部区域结合良好,没有发现超标缺陷,周边局部未复合区在20~100mm之间,
属于爆炸焊接过程边界效应区。
对轧制后的复合板进行550℃×1.5h退火,退火后取样测试,取样位置见图1。表2所示是复合板正常区
域和异常区域钛板的性能,不同区域的强度均高于理论强度;内部正常区域的剪切强度高于196MPa,强度波
动较小,说明复合板各区域结合强度较均匀;而边部有几组剪切强度不均匀,部分数据低于140MPa,不满足
GB/T8547—2006中其他类复合板要求[4],后续加工时,复合板出现分层的可能性较大。
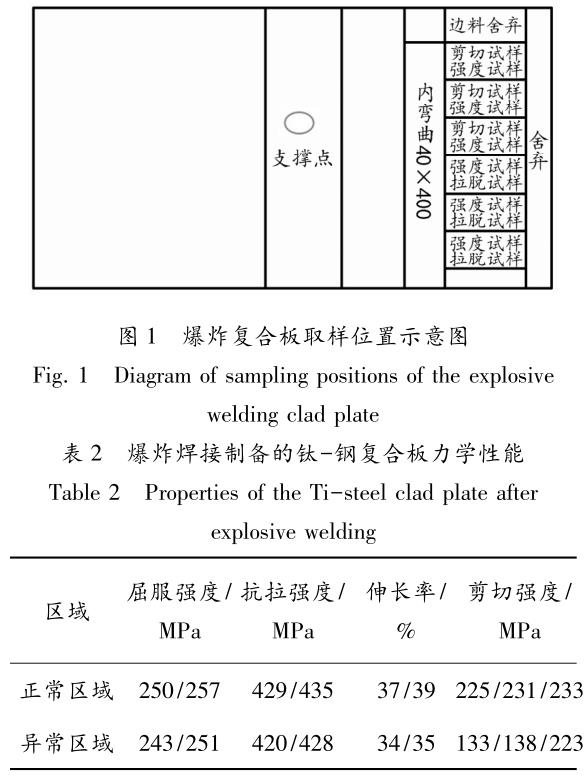
2.2爆炸焊接+热轧钛-钢复合板缺陷
采用爆炸焊接+热轧工艺制备TA1/Q235B钛-钢复合板,钛板头尾和边部区域出现分层、碎边与皱褶等缺
陷,见图2。对于爆炸焊接钛-钢复合板,边界效应普遍存在,会显著降低复合板结合面的结合强度和复合
率[5],而除了边界效应造成的缺陷外,分层和碎边缺陷会影响成品率。
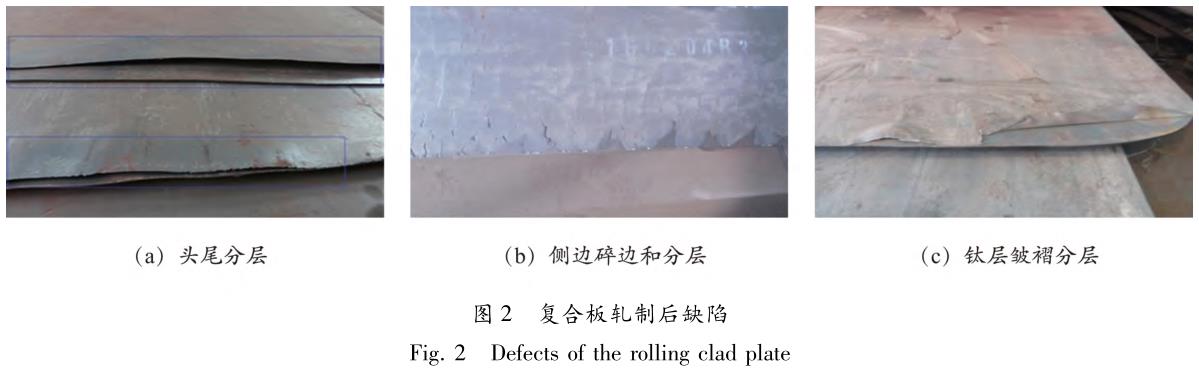
2.3钛板表面缺陷对复合板性能影响
为了分析复合板产生分层和碎边等缺陷的原因,重点对钛板的组织和性能进行分析。
图3所示是TA1/Q235B复合板爆炸焊接+热轧后,缺陷附近位置的界面微观形貌。可以看到,在钛复合板
一侧有明显的裂纹、孔洞、夹杂物和不均匀变形区域等。钛板中的这些缺陷接近表面区域,可能是由于原材
料板坯或半成品缺陷修磨去除不干净,产生缺陷遗传,造成钛板表面夹杂、富氧层和疏松等缺陷,进而在轧
制中发生压入和扩展。
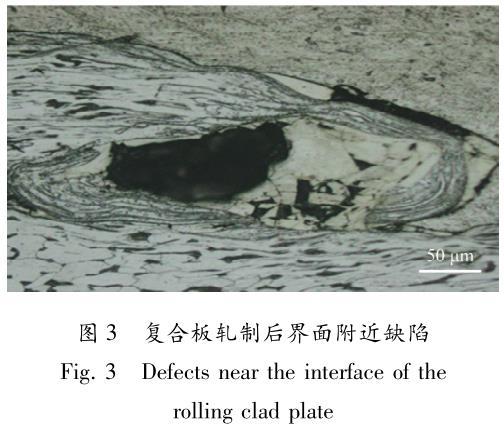
图4所示是复合板热轧后钛板的局部表面缺陷,存在与基体分层的白亮缺陷、与基体连接紧密的较亮缺
陷。分层的白亮区域局部最大厚度超过300μm,与基体连接较紧密的较亮区域局部最大厚度超过200μm,主
要为氧化层。爆炸焊接复合用钛板需要进行退火+喷砂+酸洗+抛光,减薄量一般在200μm左右,因此,钛板
表面缺陷过厚时,成品中存在氧化层残留。
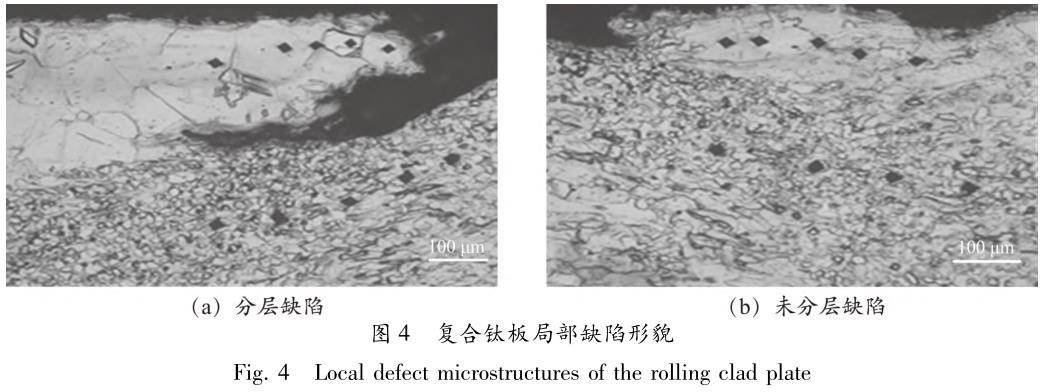
表3所示是图4中不同区域的硬度测试结果。分层的白亮区硬度最高,未分层的较亮区域硬度也较高,过
渡区域硬度次之,正常区域硬度最低。分析确认,表面硬度偏硬区域为氧化层,接近表面区域为富氧层,硬
度也高于正常区域的。
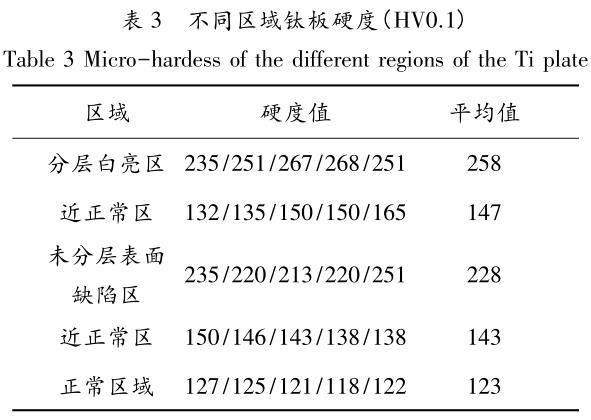
图5是复合用钛板表面的局部微裂纹和分层缺陷,在后续的爆炸焊接中,这些缺陷会进一步引起分层和
结合不牢等缺陷。
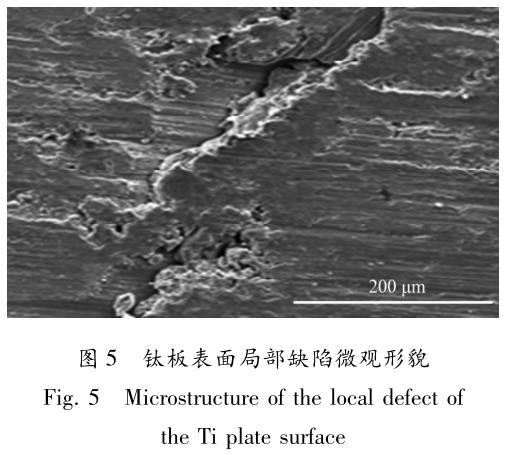
2.4热压对钛板表面的影响
钛板屈服强度越大,爆炸焊接过程中钛板应变强化越明显,塑性变形能力减弱,易形成褶皱性缺陷。通
过控制原材料钛板的屈服强度可使之处于较低的水平,在爆炸焊接时形成稳定、连续的塑性变形[6]。
退火时温度在600℃以上时,每提高50℃,纯钛的屈服强度会下降10MPa左右。鉴于此,爆炸焊接前,钛
板应在厚钢板压制下进行长时间热压校形,以获得良好的性能和板形。但热压温度增高会增加钛板表面的氧
化层厚度,因此,应设计适宜的退火温度以降低钛板的屈服强度,避免产生过厚(大于200μm)的氧化层。
图6所示是650℃和750℃热压后钛板的表面形貌,中间的灰黑色区域是钛板叠压贴合造成的结果,边部
氧化剧烈,温度高时钛板软化造成贴合更紧密,氧化和高温扩散也更显著。
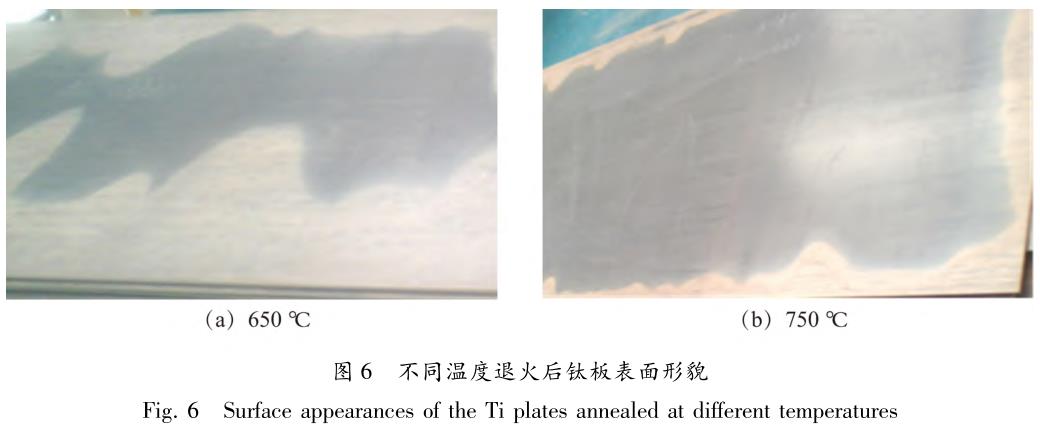
钛在高温下与氧、氮等元素剧烈反应,表面形成较厚的吸气层,硬度升高、塑性降低。图7是钛板边部
区域在650℃和750℃热压后表面情况,检测吸气层厚度分别为50~100μm和80~150μm。钛板热压后边部区
域比中间区域的氧化更明显,存在不均匀现象,温度越高氧化层越致密、越厚,需反复多次喷砂酸洗清除氧
化层,可能造成板形不良及加工硬化,不利于爆炸焊接。
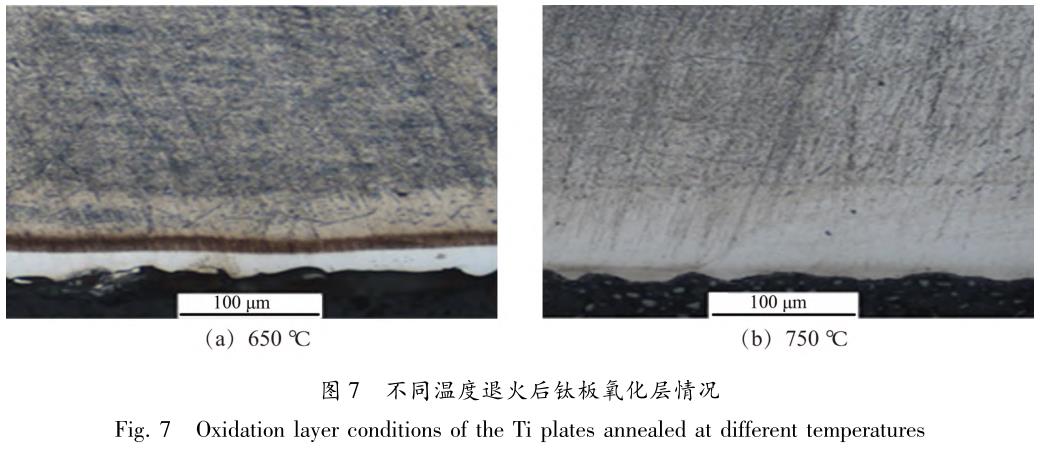
2.5分析与讨论
爆炸焊接用钛板热压后表面氧化层可以通过喷砂、酸洗等工序正常去除,但由于原料、熔炼和钛材轧制
加工中一些不可避免的因素,钛材表面的夹杂、富氧层和疏松等缺陷在轧制中发生较深的压入和扩展,造成
钛板局部残留氧化层等缺陷。热压钛板温度越高,氧化层越致密、越厚,反复多次喷砂、酸洗可能造成板形
不良及加工硬化,不利于爆炸焊接。
3、结论
(1)利用爆炸焊接+热轧工艺制备的TA1/Q235B复合板,出现了碎边、分层和皱褶分层等缺陷,这与爆炸
焊接后复合板边部局部区域剪切强度低于140MPa、结合不牢固有关。
(2)钛-钢复合板轧制后钛侧出现的碎边、分层和皱褶等缺陷,与钛板的板形不良和表面的氧化吸气层
厚度较大关系密切。为消除氧化层残留,需要选用优质钛锭,板坯和半成品表面缺陷修磨要彻底;选用适宜
的热压温度,爆炸焊接前对钛板进行抛光,去除表面氧化吸气层,以减少复合时的结合不良问题。
参考文献:
[1]宋磊,邹见宾,李松元,等.钛/钢
爆炸复合板边界效应的产生与预防[J].有色金属工程,2015,5(2):1-3.
[2]王小华.电厂烟囱用钛-钢复合板钛
复材焊接缺陷产生原因及预防措施[J].材料开发与应用,2012,27(4):102-105.
[3]辛宝,岳宗洪,邓光平,等.钛-钢
复合板热轧工艺研究[J].材料开发与应用,2016,31(6):75-79.
[4]国家质量监督检验检疫总局,中国
国家标准化管理委员会.钛-钢复合板:GB/T8547—2006[S].北京:中国标准出版社,2006.
[5]王飞,刘广初,王连来.减小爆炸焊
接边界效应影响研究[J].工程爆破,2005,11(2):6-9.
[6]辛宝,刘金涛,崔卫超,等.钛的屈
服强度对大面积钛-钢复合板结合性能的影响[J].材料开发与应用,2015,30(6):10-14.
相关链接