表面完整性是对零件加工后表面微观几何特征和表面层在一定深度范围内物理力学特性变化的总体描述,主要包括表面粗糙度、表面微观形貌、表面显微硬度、表面残余应力及显微结构等指标[1],大量学者对表面完整性与试件疲劳寿命之间的关系进行了研究。一般认为,表面微观几何形貌形成的微观应力集中对试件的疲劳寿命具有较大的影响,表面越粗
糙,应力越集中,零件的疲劳寿命越低[2-4]。Ås 等[5]与 Andrews 等[6]学者认为,表面粗糙度和表面微观形貌主要通过应力集中系数影响疲劳寿命。Neuber 等[7]研究发现,随着应力集中系数的增大,试件的疲劳性能会逐渐降低。Kawagoishi 等[8]认为,试件表面产生的残余压应力能够抑制表面裂纹的产生和扩展,从而提升试件的抗疲劳性能。Syed 等[9]认为,残余拉应力会提升裂纹的扩展速率,从而降低疲劳寿命。杨茂奎等[10]研究发现,残余应力在实际工作环境下存在不同程度的释放,进而改变表面残余应力对零件疲劳性能的影响程度。杨茂奎等[10]、任敬心等[11]、张建龙等[12]分别针对 GH4169、GH33A、304 不锈钢 3 种不同材料的研究表明,表面硬度对材料疲劳性能的影响会因实验材料、外加载荷形式、表面应力状态、试验温度、加工硬化程度等因素的变化而变化。Josefson 等[13]认为,加工表面塑性变形层可细化表层组织,提高材料的屈服强度,增加表面硬度,阻止位错线向表面延伸,从而提高试件的疲劳强度。Suárez 等[14]和 Li 等[15]分别通过超声辅助切削 GH4169 和 TC4,并与传统切削进行了对比研究,结果均表明,塑性变形程度的增加可以提高疲劳寿命。Li 等[16]研究了塑性变形程度对疲劳寿命的影响,认为较大的表面塑性变形能够提高试件的高周疲劳性能,但对试件低周疲劳性能具有消极影响。

目前,国内外学者针对不同材料的各项表面完整性指标对疲劳寿命的影响进行了大量研究,但是针对表面塑性变形层中纤维组织方向对试件疲劳性能的影响规律及其机理的研究尚不充分。由于车削与铣削的加工机制不同,因此在加工疲劳试件时,车削加工塑性变形层中组织纤维化变形沿试件的周向,而铣削加工塑性变形层中组织纤维化变形沿试件的轴向。当承受沿着轴向的交变载荷时,2 种不同方向的塑性变形层对试件疲劳性能的影响存在差异。文中试验以车削和铣削加工为基础,使钛合金 TC4 疲劳试件表面塑性变形层中分别产生垂直和平行于轴向加载方向的纤维组织,通过控制加工参数,在车削试件表面完整性指标基本优于铣削试件的情况下,研究加工表面塑性变形层中组织纤维化变形方向对试件疲劳寿命的影响,拟为零件加工方式的选择提供借鉴。
1 、试验
1.1 材料
钛合金 TC4 是一种典型 α+β 钛合金,具有比强度高、耐腐蚀、耐高温及焊接性好等优良特性,在航空航天、医疗器械、交通运输等领域得到广泛应用[17-18]。
由于钛合金 TC4 的导热率低、屈强比高、塑性变形范围窄小,因此在机械加工过程中,刀具刃口附近切削产生的热量不易散失,刀具磨损较为严重,从而出现零件加工效率低、成本高、质量难以保证等问题[19]。文中试验选用的钛合金 TC4 材料的化学成分组成及在室温下的力学性能如表 1—2 所示。
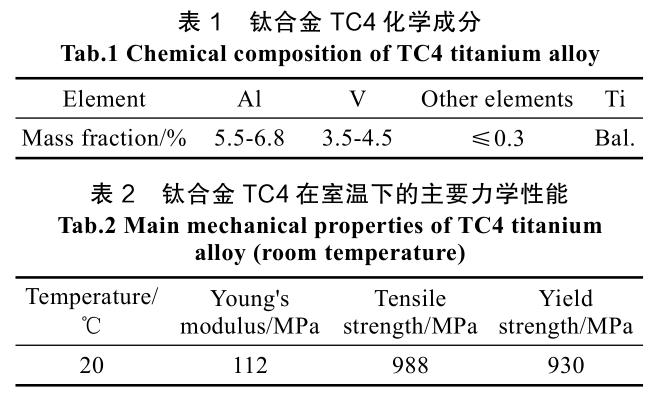
1.2 试件加工方案
疲劳测试试件的设计参考 GB/T 3075—2021《金属材料 疲劳试验 轴向力控制方法》[20],疲劳测试段为直线段,长度为 6 mm,加工完成后试件的直径为5 mm。分别采用车削和铣削的加工方式对疲劳测试件进行加工。车削加工和铣削的加工方案分别如图 1—2 所示。
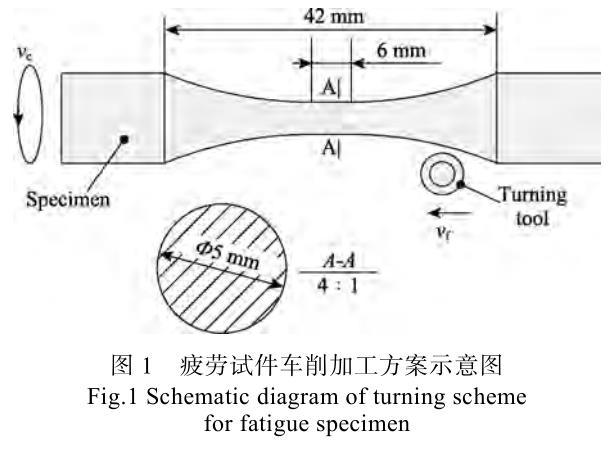
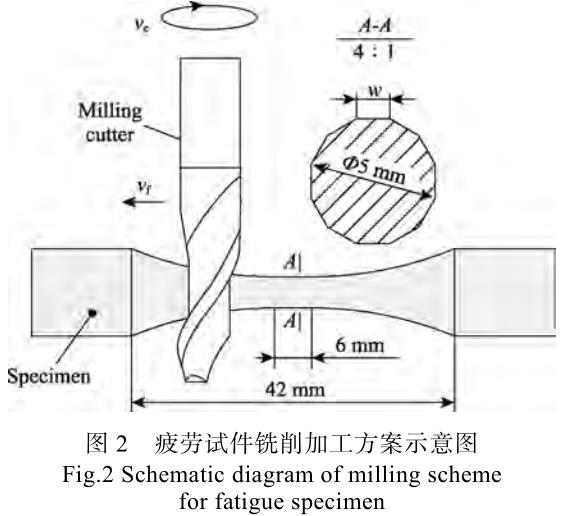
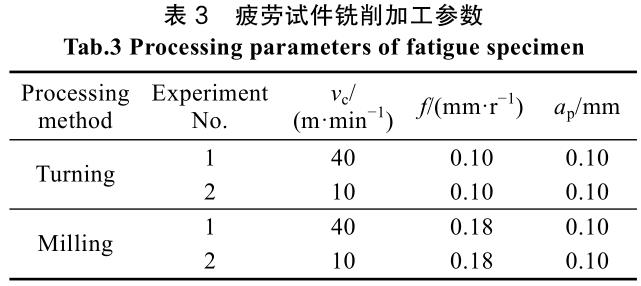
为了保证经车削加工和铣削加工后试件表面具有一致的表面微观几何形貌,试件的车削加工采用圆形车刀片,刀片直径为 8 mm,前角为 0°,后角为 15°;试件的铣削加工采用单刃立铣刀,刀具直径为 8 mm,刃长为 25 mm,全长为 75 mm,螺旋角为 45°。采用水基切削液对刀具和试件进行冷却和润滑。由于铣削和车削的加工机制不同,在车削加工时工件跟随主轴旋转,因此车削加工得到的疲劳试件的截面为圆形。
在铣削加工时,铣刀跟随主轴旋转,工件被固定在第4 轴上,首先铣刀完成 1 次走刀后返回原位,紧接着第 4 轴转动 6°,之后循环上述过程。该过程循环 60次后便形成铣削疲劳试件的表面,因此铣削加工得到的疲劳试件截面不是圆形,而是一个边长 w=0.26 mm的标准正六十边形,这样的疲劳试件可以避免传统板状铣削试件在过渡圆弧处存在的毛刺及应力集中等不稳定因素对疲劳性能产生额外的影响[21]。疲劳试件的加工参数如表 3 所示。为了确保加工的可靠性,每个试件均采用新刀进行加工。
2、 表面完整性测试
2.1 表面粗糙度
利用 TIME 3220 型触针式表面轮廓测量仪对试件 加 工 表 面 粗 糙 度 进 行 测 量 。 设 置 取 样 长 度 为0.8 mm,评定长度为 4 mm,方向沿试件的轴向。表面粗糙度测试结果如图 3 所示。车削试件的表面粗糙度分别为 Ra 0.26 μm 和 Ra 0.24 μm,铣削试件的表面粗糙度分别为 Ra 0.41 μm 和 Ra 0.39 μm。表面粗糙度主要与刀具的半径和进给量有关,在进给量相同时,同一种加工方式的试件表面粗糙度相差不大。这里车削和铣削采用的刀具半径均为 8 mm,铣削加工采用的进给量较大,在已加工表面上由于断续切削所产生的残留部分的高度较高,从而导致表面粗糙度增大,因此车削试件的表面粗糙度明显小于铣削试件的表面粗糙度。
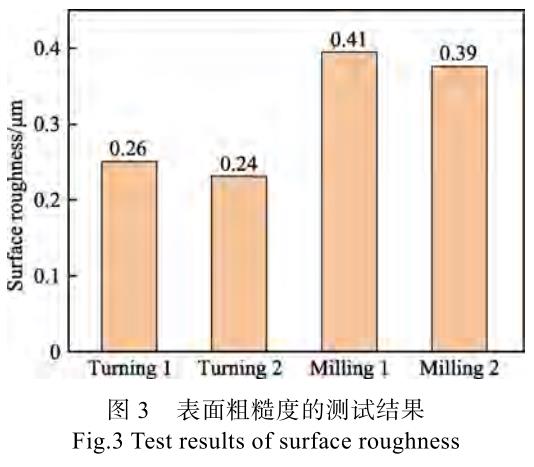
2.2 表面显微硬度
表面显微硬度采用 FUTURE–TECH FM–800 型显微硬度计进行测量,测量时加载载荷为 1.96 N,载荷的保持时间为 10 s。试件表面显微硬度的测试结果如图 4 所示。车削试件表面显微硬度的均值分别为366.1HV 和 370.6HV,铣削试件表面显微硬度的均值分别为 352.6.5HV 和 366.4HV,车削试件的表面显微硬度略大于铣削试件。表面显微硬度是加工中机械效应与热效应共同作用的结果,实验选取的钛合金 TC4材料的基体硬度为 297HV。经过车削和铣削加工后,试件的表面显微硬度均大于基体的硬度,存在明显的加工硬化现象,表面硬化可以提升表层材料的承载能力,阻碍位错运动,抑制疲劳裂纹的扩展,从而提升试件的疲劳寿命。
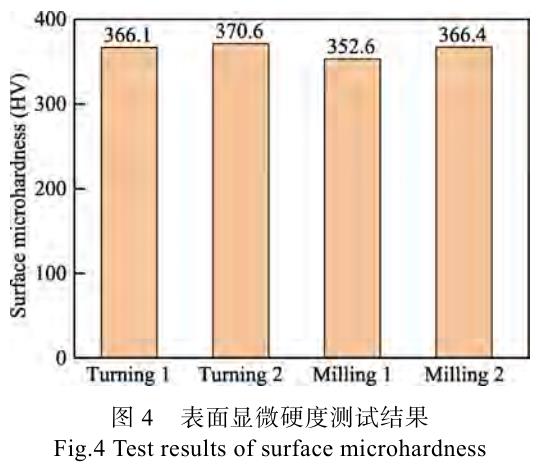
2.3 表面残余应力
使用 AutoMATE Ⅱ型 X 射线衍射应力仪对试件表面沿轴向的残余应力进行测量,表面残余应力测试结果如图 5 所示。2 种加工方式得到的疲劳试件表面残余应力均为压应力。车削试件的残余应力分别为−581 MPa 和−531 MPa,铣削试件的残余应力分别为−103 MPa 和−88 MPa。与表面硬度的形成机制类似,表面残余应力同样是加工时机械效应与热效应共同作用的结果,车削试件与铣削试件表面残余应力的数值呈现出如此大的差异,这在很大程度上是因加工方式的不同。残余压应力可以在试件承受交变载荷时抵消部分拉应力,从而抑制裂纹的产生和扩展,进而提升试件的抗疲劳性能。残余压应力越大对试件疲劳性能的提升效果越明显。
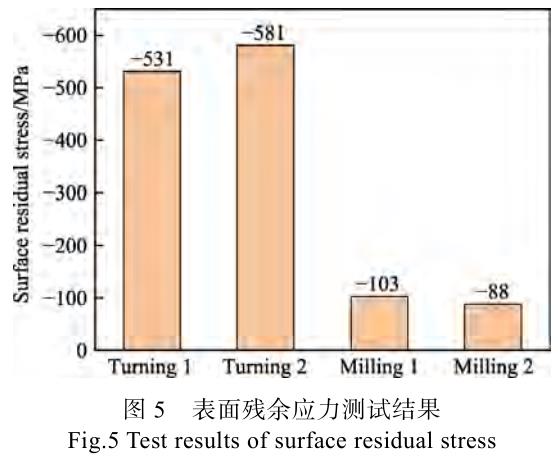
2.4 表面微观形貌
试件表面二维、三维形貌采用基恩士 VHX–5000型超景深三维显微镜进行观测,结果如图 6 所示。在疲劳试件的加工过程中,车削和铣削加工的进给方向均沿着试件的轴向。在试件的轴向方向均可观察到周期性的波峰和波谷。由于 2 种加工方式中采用的进给量不同,因此相邻的波峰或波谷间的距离也不同。车削的进给量 f=0.10 mm/r,铣削的进给量 f= 0.18 mm/r,在三维形貌中可以清楚地观察到铣削表面相邻波峰或波谷之间的距离大于车削表面相邻波峰或波谷之间的距离。
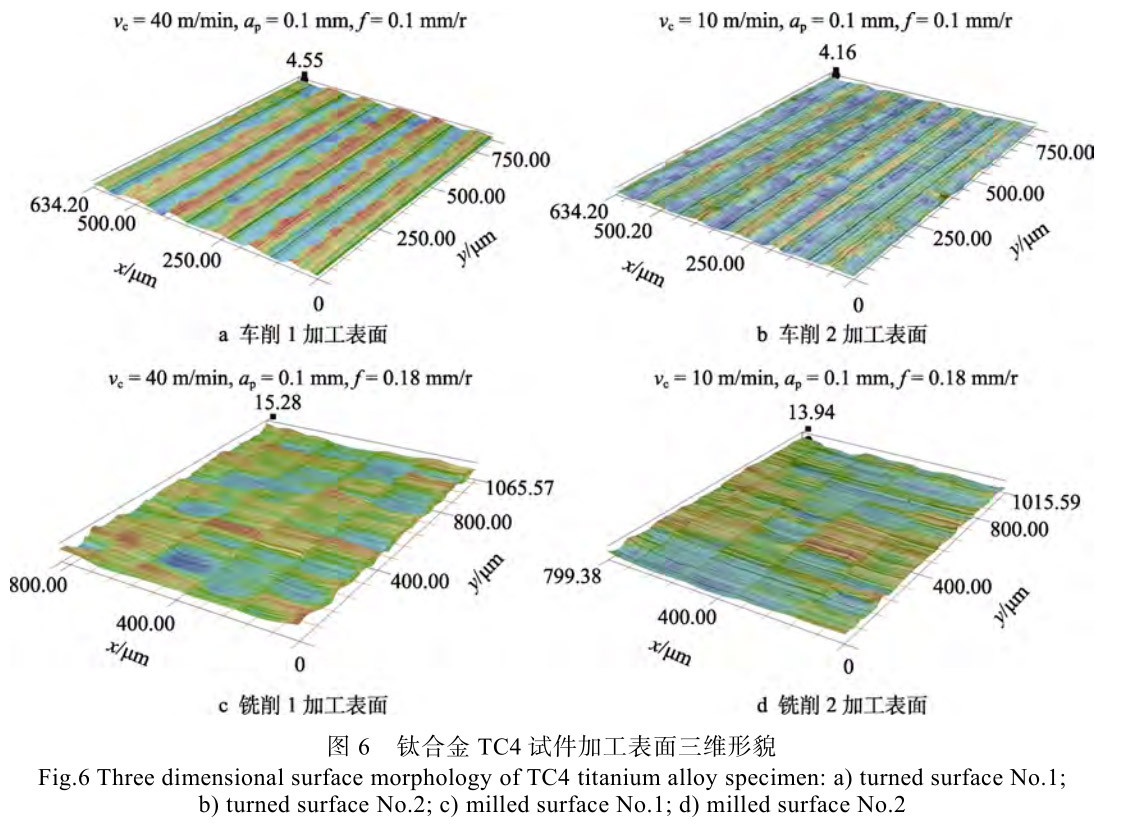
为了尽可能保持 2 种加工方式得到的疲劳试件表面形貌一致,在试验方案设计阶段均采用直径为8 mm 的刀具。由此可见,在理论上 2 种试件轴向表面形貌轮廓的谷底圆半径应一致。在加工过程中,由于刀具几何轮廓的变化、加工系统的振动及积屑瘤的影响,试件已加工表面存在很多沿着切削速度方向的微观划痕。在加工时,刀具进给方向均沿着试件的轴向,由于 2 种加工方式切削速度的方向不同,因此微观划痕的方向也不同,车削加工产生的划痕垂直于进给方向,而铣削加工则平行于进给方向,如图 7 所示。一般认为,车削表面的微观划痕对试件的疲劳性能具有严重的消极影响[22-23],其原因是在承受轴向的交变载荷时,垂直于载荷方向的微观划痕底部容易因应力集中而产生微裂纹,导致疲劳源在试件表面萌生,从而降低试件的疲劳寿命。
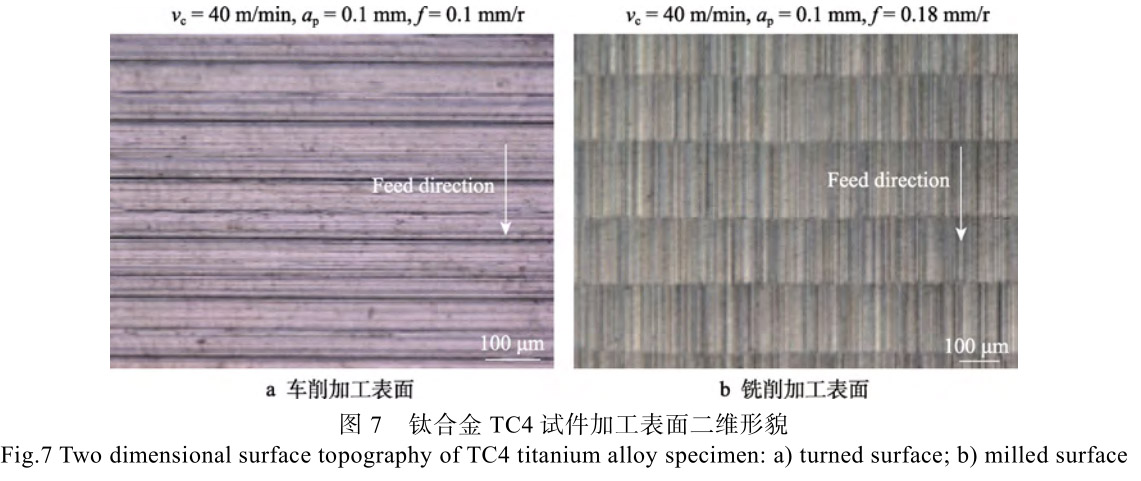
3、 疲劳性能测试及结果分析
3.1 疲劳试验方案
疲劳试验采用长春机械研究院研制的 GPS100 电磁谐振式高频拉压疲劳试验机,其所能施加的最大静载荷为 100 kN,最大动载荷为 50 kN,工作频率为80~250 Hz,加载精度≤±1%,对疲劳试件采用应力比 R=0.1 且载荷频率为 100 Hz 的正弦波单向拉伸加载方案,加载的最大应力 σmax 为 870 MPa,试件的疲劳寿命取 5 次测量的平均值。
3.2 疲劳试验结果
钛合金 TC4 的疲劳试验结果如图 8 所示。2 组车削 参 数 下 试 件 的 平 均 疲 劳 寿 命 为 8.57×104 次 和9.63×104 次,2 组铣削参数下试件的平均疲劳寿命为117.88×104 次和 472.61×104 次。铣削加工试件的疲劳寿命是车削加工试件的 12~48 倍。
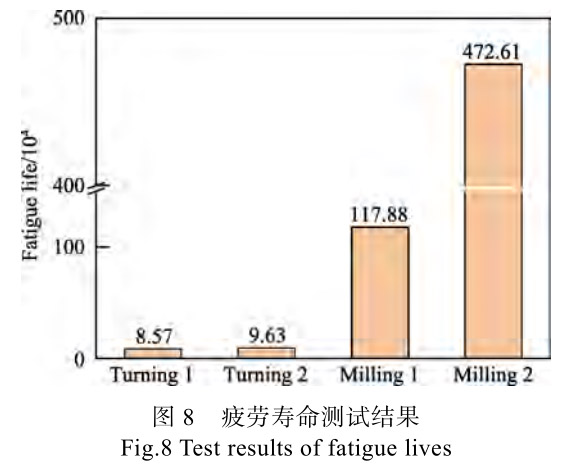
采用 ZEISS 热场发射电子显微镜对车削和铣削试件的疲劳断口形貌进行观察,如图 9 所示。疲劳断口可以主要分为 3 个区域:疲劳源、疲劳裂纹扩展区、疲劳瞬断区。结果表明,所有试件断口的疲劳源均成核于亚表面(30~90 μm),而非试件的表面,这表明2 种加工方式在试件表面产生的不同方向的微观划痕未对疲劳裂纹的萌生产生影响。
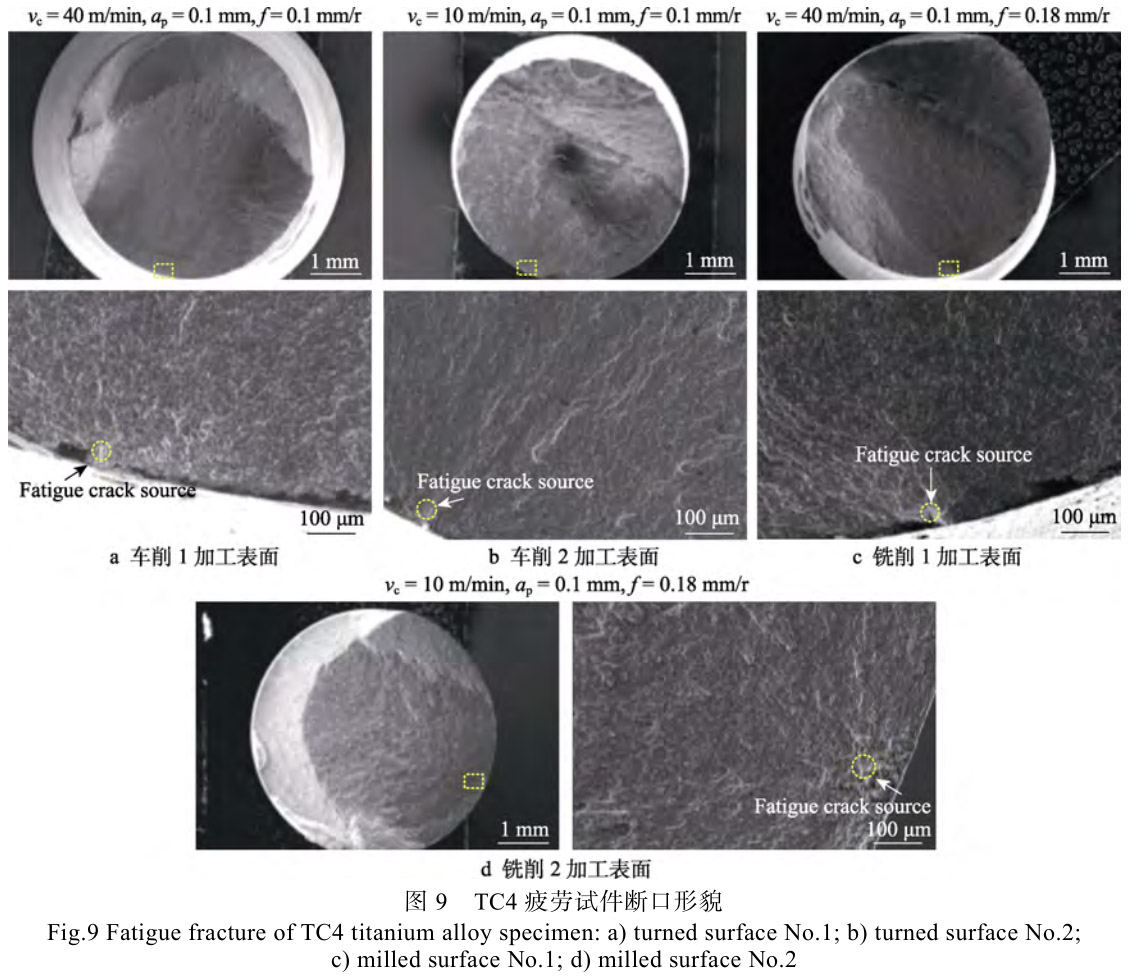
在试件亚表面的裂纹扩展区分别距疲劳源相同的距离处,对车削和铣削中编号 1 试件的断口进行疲劳条带观察,如图 10 所示。在相同的放大倍数下,铣削试件断口的疲劳条带间距小于车削试件断口的疲劳条带间距,前者约为 0.15 μm,后者约为 0.25 μm。疲劳条带是塑性区位错滑移的结果[24],其方向一般与裂纹的扩展方向垂直,每条疲劳条带均对应一次应力循环,因此铣削试件疲劳条带间距较小表明其裂纹的扩展速度更慢,在疲劳裂纹扩展阶段的抗疲劳性能更强。在整个高周疲劳试验过程中,疲劳裂纹萌生阶段寿命的占比较大,而裂纹扩展阶段较短,在高周疲劳试验过程中甚至可以忽略[25],因此铣削试件疲劳寿命大于车削试件疲劳寿命的原因主要在于前者可以抑制疲劳源的萌生,相较于车削加工可以大幅增加疲劳裂纹萌生阶段的寿命。
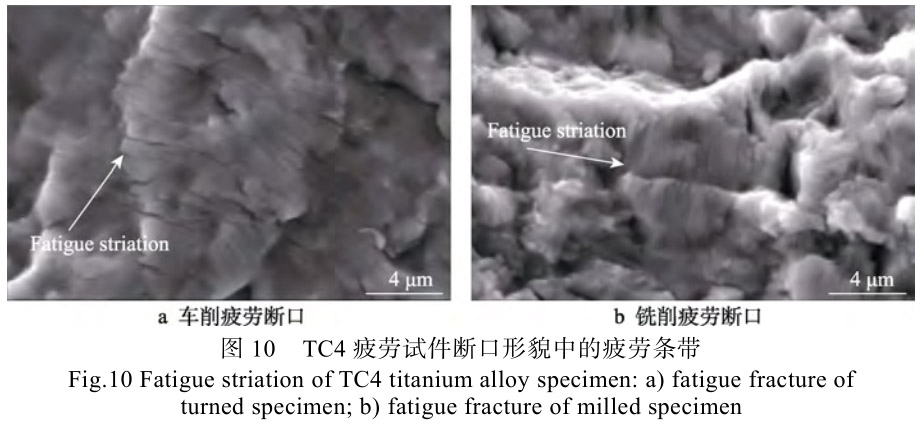
3.3 分析与讨论
将表面完整性试验结果与疲劳试验结果进行综合分析,在试验参数范围内,车削试件的表面粗糙度、表面显微硬度、表面残余压应力 3 个指标均优于铣削试件。然而,铣削加工试件的抗疲劳性能远远大于车削加工试件的抗疲劳性能。这说明表面粗糙度、表面显微硬度和表面残余应力 3 个指标的差异并非是铣削疲劳试件寿命远远大于车削疲劳试件的原因。
为了解释这一现象的原因,利用 ZEISS 热场发射电子显微镜对加工表层微观组织进行观察,得到了 2种加工方式沿试件轴向和周向的微观组织,如图 11所示。铣削试件的近表面轴向和车削试件的近表面周向(图 11b—c 所示)的塑性变形层中均可观察到明显 的 组 织 纤 维 化 变 形 , 铣 削 塑 性 变 形 层 深 度 为4.1 μm,车削塑性变形层深度为 8.6 μm。车削试件表面塑性变形层更深,并且晶粒扭曲的程度更大,组织纤维化现象更加明显。2 种加工方式下,在试件的亚表面均未观察到夹杂、裂纹、空穴等缺陷,可以排除
因加工带来的亚表面损伤对试件疲劳性能产生的不良影响。结合疲劳源位置的分析可以认为,试验中车削和铣削加工在试件表面产生的微观划痕方向的不同并未对疲劳寿命产生实质性的影响。塑性变形是机械加工中机械效应与热效应共同耦合的结果,当刀具后刀面与已加工表面之间进行摩擦和挤压时产生的应力大于材料本身的屈服强度时,表层的材料便会沿切削力方向发生塑性变形,从而形成塑性变形层。在塑性变形层中可以观察到沿刀具切削速度方向的组织纤维化变形,原本的晶粒被扭曲和拉长,在试件承受载荷时可以抑制裂纹的萌生和扩展,阻碍位错继续运动,从而提升试件的疲劳强度。
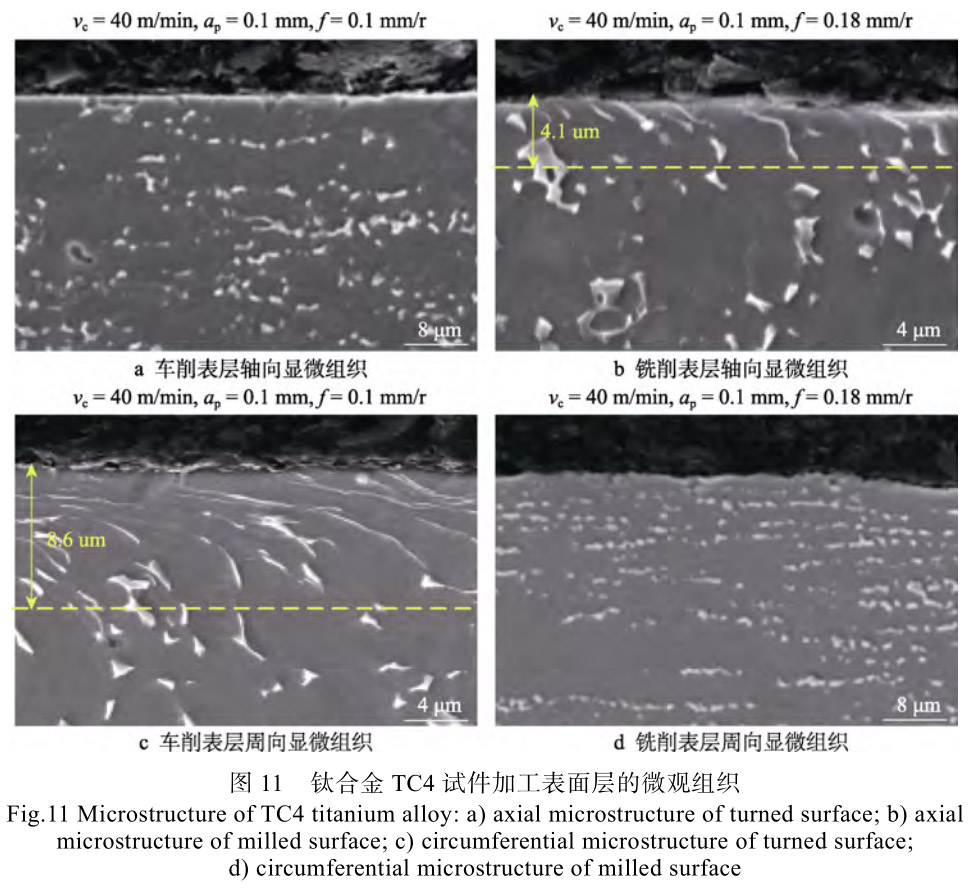
车削和铣削 2 种加工方式的切削速度方向不同,因此2 种加工方式所得表面塑性变形层的组织纤维化方向也不同,车削加工的疲劳试件表面纤维化方向沿试件的周向,而铣削加工的疲劳试件表面纤维化方向沿试件的轴向。当试件承受轴向的交变载荷时,铣削试件表面沿着载荷方向的表面纤维化变形对疲劳裂纹萌生和扩展的抑制效果强于车铣削加工,可以有效地提升试件的抗疲劳性能。通过对表面粗糙度、表面显微硬度、表面残余应力、表面微观形貌及疲劳断口进行相关测试和分析,未能确定导致车削与铣削试件疲劳寿命之间存在巨大差距的原因,因此可以认为导致该差距的主要原因是塑性变形层中组织纤维化方向的不同,并且相较于垂直于载荷方向的组织化纤维变形,沿着载荷方向的组织纤维化变形抑制疲劳裂纹的萌生和扩展的效果更加明显,在很大程度上提升了试件的抗疲劳性能,这也是铣削试件疲劳寿命远大于车削试件的主要因素。
4、 结论
1)车削和铣削加工表面的微观组织都会沿切削速度方向形成纤维化塑性变形。由于加工机制的不同,车削加工形成的组织纤维化方向沿疲劳试件的周向,铣削加工形成的组织纤维化方向沿试件的轴向。
2)当车削加工试件的表面完整性指标基本优于铣削加工试件时,铣削加工试件的轴向抗疲劳性能是车削加工试件的 12~48 倍。在承受轴向交变载荷时,铣削加工形成的沿试件轴向的纤维组织能够抑制疲劳裂纹的萌生和扩展,大幅提升试件的抗疲劳性能,并且提升效果主要来源于对疲劳裂纹萌生的抑制。
3)在满足试件加工表面质量设计要求的前提下,应尽可能选择切削速度方向与试件承载方向相同的加工方式,从而使机械加工塑性变形层中纤维组织的方向与交变载荷的方向相同,进而提高试件的抗疲劳性能。
参考文献:
[1]王尚志. 航空零件加工的表面完整性[J]. 航空工艺技术, 1988, 31(2): 31-33.
WANG Shang-zhi. Surface Integrity of Aviation Parts Processing[J]. Aeronautical Manufacturing Technology,1988, 31(2): 31-33.
[2]AROLA D, WILLIAMS C L. Estimating the Fatigue Stress Concentration Factor of Machined Surfaces[J].International Journal of Fatigue, 2002, 24(9): 923-930.
[3]谭靓, 姚倡锋, 张定华. 7055 铝合金高速加工表面完整性对疲劳寿命的影响[J]. 机械科学与技术, 2015, 34(6):872-876.
TAN Liang, YAO Chang-feng, ZHANG Ding-hua. In-fluence of the Surface Integrity on the Fatigue Life for High-Speed Milling of 7055 Aluminum Alloy[J]. Me-
chanical Science and Technology for Aerospace Enginee-ring, 2015, 34(6): 872-876.
[4]武导侠, 张定华, 姚倡锋. GH4169 高温合金车削表面完整性对疲劳性能的影响[J]. 航空材料学报, 2017,37(6): 59-67.
WU Dao-xia, ZHANG Ding-hua, YAO Chang-feng. Effect of Surface Integrity of Turned GH4169 Superalloy on Fatigue Performance[J]. Journal of Aeronautical Mate-
rials, 2017, 37(6): 59-67.
[5]ÅS S K, SKALLERUD B, TVEITEN B W. Surface Rou-ghness Characterization for Fatigue Life Predictions Using Finite Element Analysis[J]. International Journal of
Fatigue, 2008, 30(12): 2200-2209.
[6]ANDREWS S, SEHITOGLU H. A Computer Model for Fatigue Crack Growth from Rough Surfaces[J]. Interna-tional Journal of Fatigue, 2000, 22(7): 619-630.
[7]NEUBER H. Theory of Notch Stresses: Principles for Exact Calculation of Strength with Reference to Structural form and Material[M]. Berlin: Springer-verlag, 1958:
204.
[8]KAWAGOISHI N, CHEN Q, KONDO E, et al. Influence of Cubic Boron Nitride Grinding on the Fatigue Strengths of Carbon Steels and a Nickel-Base Superalloy[J]. Journalof Materials Engineering and Performance, 1999, 8(2):152-158.
[9]SYED A K, AHMAD B, GUO Hua, et al. An Experimen-tal Study of Residual Stress and Direction-Dependence of Fatigue Crack Growth Behaviour in As-Built and Stress-Relieved Selective-Laser-Melted Ti6Al4V[J]. Materials Science and Engineering: A, 2019, 755: 246-257.
[10]杨茂奎, 任敬心. 加工表面完整性对 GH4169 高温合金疲劳寿命的影响[J]. 航空精密制造技术, 1996, 32(6):28-31.
YANG Mao-kui, REN Jing-xin. Effect of Machined Sur-face Integrity on Fatigue Life of GH4169 Superalloy[J].Aviation Precision Manufacturing Technology, 1996,
32(6): 28-31.
[11]任敬心, 黄奇, 张智龙, 等. 机械加工表面完整性对高温合金材料 GH33A 疲劳寿命的影响[J]. 航空工艺技术, 1991, 34(5): 2-5.
REN Jing-xin, HUANG Qi, ZHANG Zhi-long, et al.Effect of Machining Integrity on Fatigue Life of High Temperature Alloy GH33A[J]. Aeronautical Manufac-
turing Technology, 1991, 34(5): 2-5.
[12]张建龙, 薛河, 崔英浩, 等. 加工硬化对 304 不锈钢应力腐蚀裂纹裂尖力学性能的影响[J]. 材料导报, 2019,33(24): 4147-4151.
ZHANG Jian-long, XUE He, CUI Ying-hao, et al. Effect of Work Hardening on Mechanical Properties of Stress Corrosion Crack Tip of 304 Stainless Steel[J]. Materials
Reports, 2019, 33(24): 4147-4151.
[13]JOSEFSON B L, STIGH U, HJELM H E. A Nonlinear Kinematic Hardening Model for Elastoplastic Defor-mations in Grey Cast Iron[J]. Journal of Engineering
Materials and Technology, 1995, 117(2): 145-150.
[14]SUÁREZ A, VEIGA F, DE LACALLE L N L, et al.Effects of Ultrasonics-Assisted Face Milling on Surface Integrity and Fatigue Life of Ni-Alloy 718[J]. Journal of
Materials Engineering and Performance, 2016, 25(11):5076-5086.
[15]LI Xun, YANG Shen-liang, LU Zheng-hui, et al. Influen-ce of Ultrasonic Peening Cutting on Surface Integrity and Fatigue Behavior of Ti-6Al-4V Specimens[J]. Journal of Materials Processing Technology, 2020, 275: 116386.
[16]LI Xun, GUO Zhi-yuan, YANG Shen-liang, et al. Study on the Effect of Milling Surface Plastic Deformation on Fatigue Performance of 20Cr and TC17 Specimens[J].Metals, 2022, 12(5): 736.
[17]胡伟楠. 钛合金 TC4 高速切削加工性试验研究[D]. 沈阳: 沈阳理工大学, 2020: 4-7.
HU Wei-nan. Experimental Study on High Speed Machi-ning Performance of Ttitanium Alloy TC4[D]. Shenyang:Shenyang Ligong University, 2020: 4-7.
[18]鲁媛媛, 马保飞, 刘源仁. 固溶处理温度对 TC4 钛合金组织和性能的影响[J]. 金属热处理, 2019, 44(6): 153-158.
LU Yuan-yuan, MA Bao-fei, LIU Yuan-ren. Effect of So-lution Treatment Temperature on Microstructure and Pro-perties of TC4 Titanium Alloy[J]. Heat Treatment of
Metals, 2019, 44(6): 153-158.
[19]邵明辉, 喻秋, 李顺才, 等. TC4 钛合金高速车削温度与 车 削 振 动 特 性 的 试 验 研 究 [J]. 现 代 制 造 工 程 ,2019(12): 1-8.
SHAO Ming-hui, YU Qiu, LI Shun-cai, et al. Experimen-tal Study on Turning Temperature and Turning VibrationCharacteristics of TC4 Titanium Alloy under High SpeedTurning[J]. Modern Manufacturing Engineering, 2019(12):1-8.
[20]GB/T 3075—2021, 金属材料 疲劳试验 轴向力控制方法[S].GB/T 3075-2021, Metallic Materials—Fatigue Testing—Axial Force-Controled Method[S].
[21]李勋, 王逸轩. 用于研究加工表面完整性影响零件拉压疲劳性能的测试件: 中国, 108267350A[P]. 2019-12-31.
LI Xun, WANG Yi-xuan. Test Piece for Researching In-fluence of Completeness of Machined Surface on Tensionand Compression Fatigue Performance of Part: CN,
108267350A[P]. 2019-12-31.
[22]LI Xun, GUAN Chun-ming, ZHAO Peng. Influences of Milling and Grinding on Machined Surface Roughness and Fatigue Behavior of GH4169 Superalloy Work-
pieces[J]. Chinese Journal of Aeronautics, 2018, 31(6):1399-1405.
[23]WU Dao-xia, ZHANG Ding-hua, YAO Chang-feng.Effect of Turning and Surface Polishing Treatments onSurface Integrity and Fatigue Performance of Nickel-
Based Alloy GH4169[J]. Metals, 2018, 8(7): 549.
[24]武永丽, 熊毅, 陈正阁, 等. 超音速微粒轰击对 TC11钛合金组织和疲劳性能的影响[J]. 材料工程, 2021,49(5): 137-143.
WU Yong-li, XIONG Yi, CHEN Zheng-ge, et al. Effect of Supersonic Fine Particle Bombardment on Microstructure and Fatigue Properties of TC11 Titanium Alloy[J]. Journalof Materials Engineering, 2021, 49(5): 137-143.
[25]翟战江, 赵琳, 彭云, 等. DP980 钢及 DP980 钢激光焊接接头的高周疲劳性能[J]. 钢铁研究学报, 2022, 34(7):679-686.
ZHAI Zhan-jiang, ZHAO Lin, PENG Yun, et al. High Cycle Fatigue Behavior of DP980 Steel and DP980 Steel Laser Welded Joints[J]. Journal of Iron and Steel Resea-
rch, 2022, 34(7): 679-686.
相关链接