引言
镍基合金GH4169具有比强度高、比刚度高和耐高温的特点,常被用于航空和航天发动机关键零部件中
,然而在加工过程中常出现崩刀、脆断、毛刺和加工效率低等现象,属于典型的难加工材料,传统的加工方
法难以满足实际生产需求。超声振动车削,又称超声振动辅助车削,从微观上看超声振动车削改变了以往普
通车削连续切割的方式,以一种断续、间歇性的方式实现对工件周期性往复运动的加工,可以在切削过程
中达到降低切削力、提高材料去除率和延长刀具寿命的效果。轴向超声振动车削是超声振动车削的一种,与
常规车削相比可以有效改善加工表面质量和降低切削力等,因此在高效精密加工方面得到了广泛的应用。
当前研究学者在对超声振动切削进行分析时,在理论分析方面研究较多,而对试验研究较少,针对航空
发动机常用材料GH4169的试验研究极少。为此,课题组选用航空发动机常用材料镍基合金GH4169为研究
对象,探究了在超声振动车削与普通车削2种加工方式下对工件的影响,为航空发动机关键零部件加工提
供试验数据。
1、试验设计
1.1试验设备
超声车削试验方案原理图如图1所示,试验所使用车床为广州数控生产的型号为GSK-980TC3-d的普通
车床。试验系统主要有日本三菱Kistlerdynamomter9272型三向力传感器、吉泰TR200型数显表面粗糙度
仪、OPTRISPIT900测温仪、超声波振动发生器,超声振动车削局部放大图如图2所示。
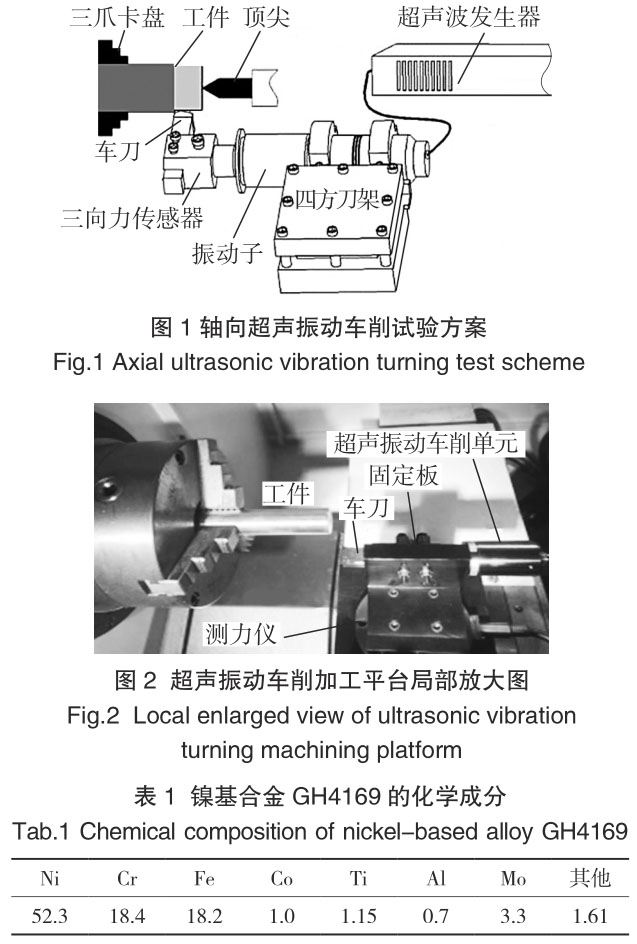
1.2工件材料
试验材料为镍基合金GH4169,实验工件采用的是直径为50mm、长度为130mm的棒料,其主要化学成
分的质量分数如表1所示。
1.3试验刀具
试验中选用日本三菱公司生产的型号为HPGX080204HTi10的硬质合金YG8涂层刀片
,该刀具的硬度和耐磨性比常规刀具高很多,刀片实物如图3所示。车刀有效几何参数如表2所示。
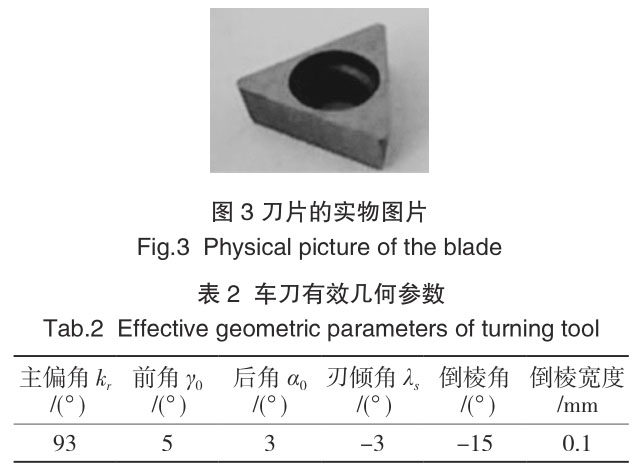
1.4切削速度的选择
进行有无轴向超声振动车削试验时,所选的切削深度ap=0.02mm,切削速度v范围为40~70mm/min,进
给量f为0.010~0.025mm/r,刀尖圆弧半径r=0.4mm,振动频率为30kHz,超声振幅为5μm,超声
切削行程为48mm。超声振动车削试验参数如表3所示[1]。
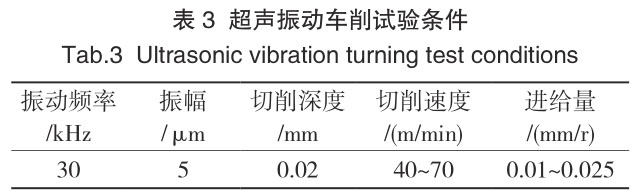
2、试验结果与分析
2.1切削力
2.1.1动态切削力
对切削力进行收集时利用上海好耐公司开发的HRsoft_DW_V2.10采集软件。2种加工方式下动态切削
力变化曲线对比如图4所示。
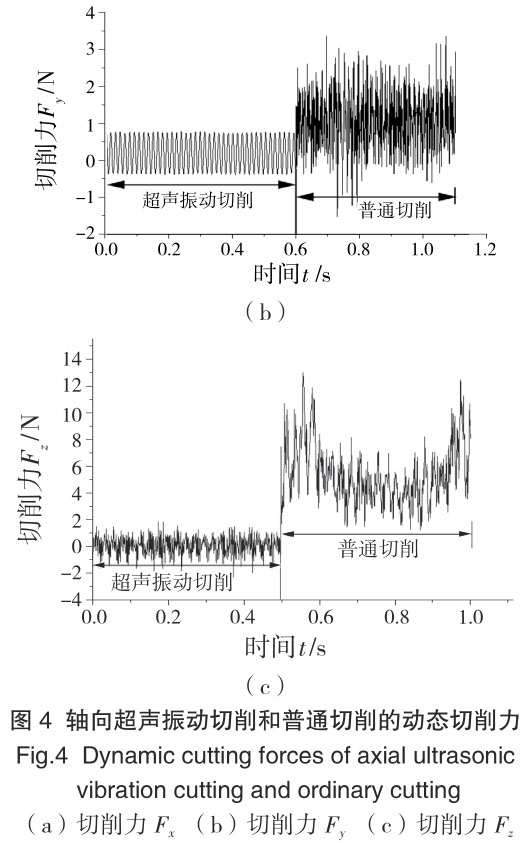
相比于普通车削的切削力变化幅度大且无规律,轴向超声振动切削时切削力的波动范围明显减小且呈周
期性,表明轴向超声切削在加工过程中能使系统稳定,提高加工精度,避免过大的切削力和切削热的产生。
2.1.2静态切削力
对试验中测力仪收集到的多组动态切削力数据求平均值,得到在不同进给量下切削力平均值随切削速度
的变化如图5所示。可以看出:轴向超声振动3方向的切削力始终小于普通车削,速度一定时,进给量增
大切削力也随之增大。进给量一定时,无论是普通切削还是轴向超声振动切削,切削力随切削速度逐渐升高
。主切削力Fz随切削速度波动性升高。因为临界超声切削速度为56.5m/min[2],在较低切削速度下超声
振动效果明显,工件与刀具之间发生明显的接触与分离,切削力大幅降低;当切削速度逐渐增大时,刀具与
工件的分离效应减弱且工件加工过程中发生热软化效应,轴向超声振动主切削力降低,逐渐趋向于普通切削
。
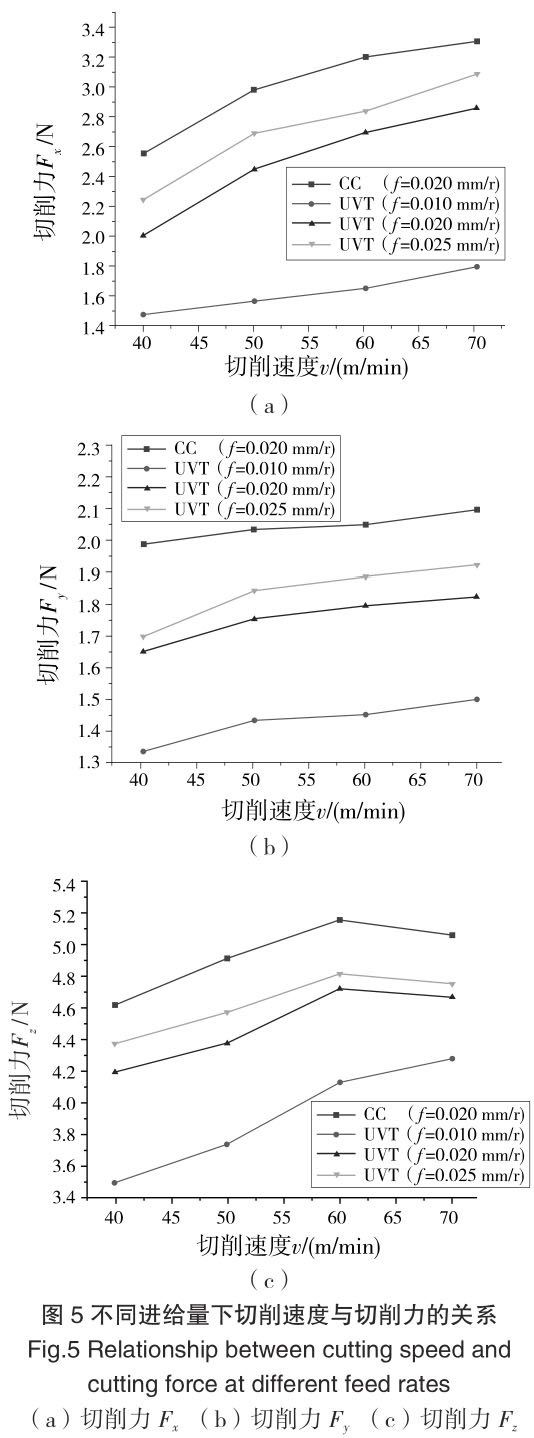
2.2切削温度
利用OPTRISPIT900测温仪对刀尖温度进行采集,为保证实验的可靠性,对每组切削速度下进行3次试
验。切削温度的变化曲线如图6所示[3]。可以看出,在相同切削速度下,切削镍基合金GH4169时,普通
车削下的切削温度比超声振动车削的切削温度要高,切削速度与切削温度呈波动性增长,这是因为在切削中
轴向超声振动切削能促使切屑折断,不会发生切屑堆积到前刀面的现象,提高散热效率;切削速度由
40m/min升高到70m/min时,切削温度最大升高了45℃[4];轴向超声振动中进给量f=0.010mm/r时
,温度变化不明显,但加工效率低;f=0.025mm/r时,温度波动较大,趋于普通车削。相比之下,f
=0.020mm/r时,在保证加工速率的情况下还能降低切削温度。
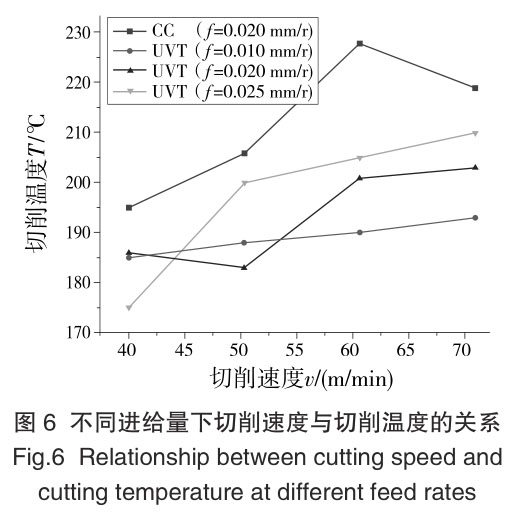
2.3工件表面粗糙度
粗糙度是精密加工中的关键指标之一。在v=40~70m/min,ap=0.02mm,A=5μm,f=30kHz和进给量f
=0.010~0.025mm/r条件下对镍基合金GH4169进行车削试验,为了保证试验的可靠性,在同一棒料上进行试
验并且每次试验均使用新的刀具,加工后的照片如图7所示,可以看出,轴向超声振动车削和普通车削加
工完成后分界线明显。
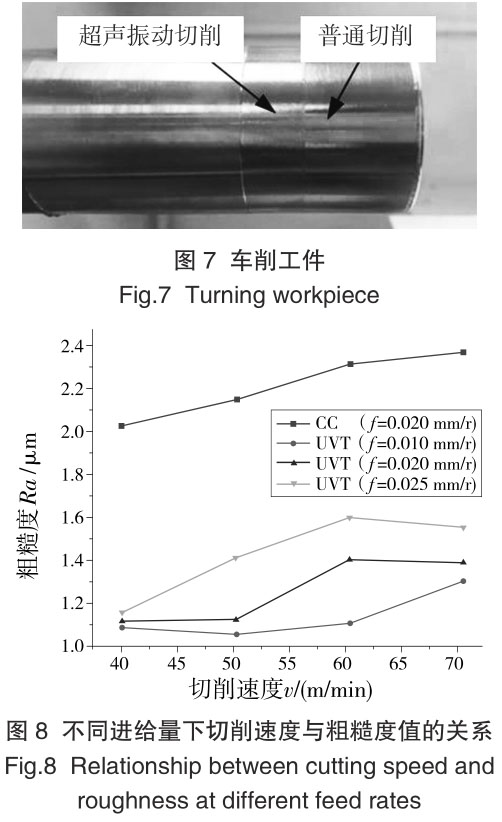
为探究2种切削方式的工件表面质量,利用TR200型数显表面粗糙度仪测量3组加工后的表面粗糙度
Ra,取平均值。切削速度对表面粗糙度值的影响如图8所示,可以看出,轴向超声振动切削的粗糙度值远
低于普通切削,切削速度一定时进给量越大粗糙度值越高。
2.4刀具磨损
为保证试验结果的准确性,收集试验用刀具并做标记,换装新刀具再次试验。车削加工完成后利用奥斯
微L208PS-3M2000显微镜对刀具的损伤情况进行观察[5]。如图9(b)、图9(c)为v=40m/min,进给
量f=0.02mm/r,ap=0.02mm、A=5μm和f=30kHz时有无超声振动切削镍基合金GH4169时刀具磨损情况。
可以看出:与普通车削相比,轴向超声振动车削能够起到减轻刀具磨损的作用。
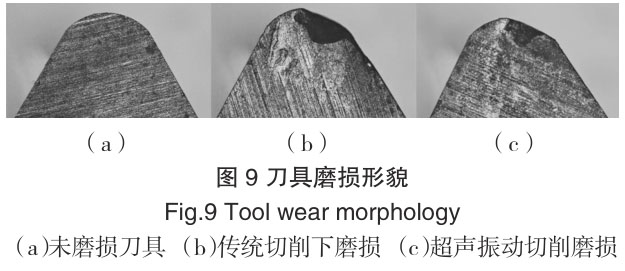
2.5切屑形貌
2.5.1宏观切屑形貌
图10为切削试验完成后收集到的切屑宏观形貌照片[6-7]。普通切削中,可清晰看到切屑边缘呈浓密
状锯齿状毛刺,如图10(a)所示,锯齿状毛刺的形成容易引起刀具和工件系统的振动,影响已加工表面的
质量。相比之下,轴向超声振动切屑边缘相对光滑,如图10(b)所示,切屑呈松卷状,切屑薄而长,不会
对加工表面造成影响。
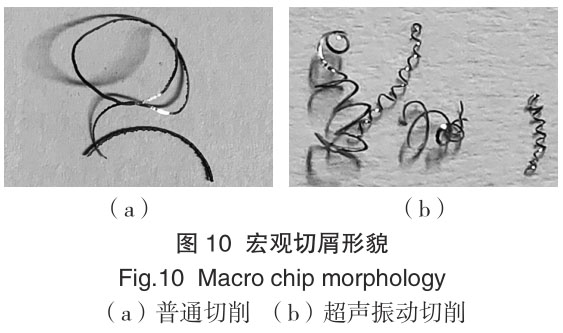
如图11为普通切削造成的积屑和轴向超声振动切削形成的碎屑。发现轴向超声振动切削可以促使切屑
发生折断,而普通切削过程中产生的切屑不易折断,容易对已加工表面造成划伤,影响工件表面质量,而轴
向超声振动的断续切削有效地避免了划伤的可能。在轴向超声振动过程中,刀具与工件周期性的接触与分离
使得切屑在瞬间被切除,所以产生细小的碎屑薄且短,不会在刀尖处堆积,因此不会对工件的加工精度产生
明显影响。
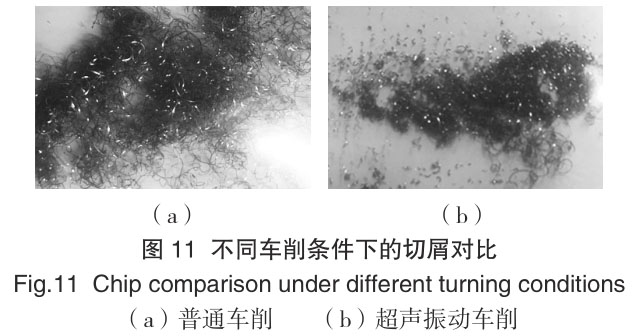
2.5.2微切屑形貌
分析切削速度对镍基合金GH4169加工中切屑形成规律的影响,利用奥斯微L208PS-3M2000金相显微
镜分别对f=0.02mm/r,ap=0.02mm条件下普通切削和轴向超声振动切削条件下所形成的切屑进行分析。
图12—图14为镍基合金GH4169放大50倍切屑微观形貌。由图12(a)、图13(a)和图14(a)可以
看出,在普通切削条件下,速度由40m/min增长到60m/min过程中,锯齿逐渐变得清晰,齿根出现裂纹,
齿根高度变大,齿根频率升高。
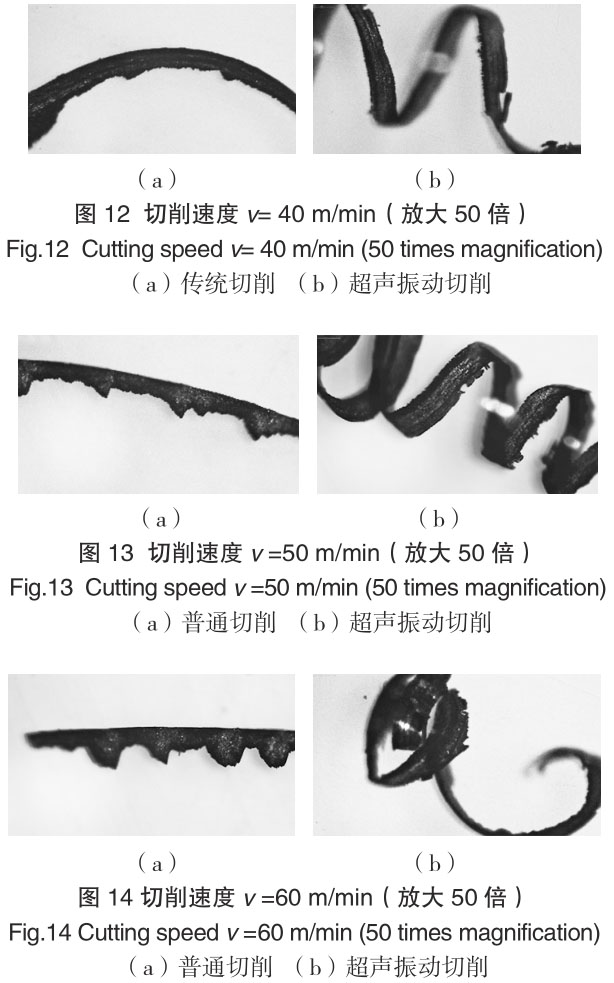
由图12(b)、图13(b)、图14(b)可以看出,在轴向超声振动切削下,锯齿化明显减小,速度由
40m/min增长到60m/min过程中切屑长度逐渐变短,缠绕程度变大,切屑有断裂的趋势。
3、结论
为探究航空航天发动机常用材料镍基合金GH4169切削参数对加工效果的影响,在进给量为0.010,
0.020,0.025mm/r条件下、切削速度为40~70m/min进行车削试验,得出了如下结论:
(1)轴向超声振动能够达到降低切削力的效果,是一种有效提高加工效率的方法,切削力与切削速度
呈波动性增长。速度一定时进给量越大切削力越大。
(2)轴向超声振动具有促使切屑折断的作用,与普通切削过程中产生的连续的带状屑不同,超声振动
切削产生的碎屑不会堆积在刀尖和刀杆上,从而避免对工件表面质量产生影响。
(3)轴向超声振动切削的温度明显低于普通切削时的切削温度,进给量f=0.010mm/r时温度变化不
明显,进给量f=0.025mm/r温度波动范围较大,有向普通车削靠近的趋势。
(4)无论轴向超声振动切削还是普通切削,工件表面粗糙度均随切削速度增大而增大,但在相同的切
削速度下,轴向超声振动粗糙度值明显减小,有效提高工件的表面质量,还可以起到减缓刀具磨损的作用。
进给量增大粗糙度降低。
参考文献
[1]郭东升,张敏良,赵森,等.超声振动车削参数对切削力的影响[J].轻工机械,2019,37
(05):29-33,38.
[2]李莹,张敏良,董慧婷,等.椭圆振动车削316L不锈钢仿真分析[J].组合机床与自动化加
工技术,2021(04):163-168.
[3]范宝朋.超声振动磨削CFRP温度场仿真及试验研究[D].南京航空航天大学,2019.
[4]叶梦力.超声振动辅助磨削碳纤维复合材料的磨削温度研究[D].武汉理工大学,2018.
[5]史于涛,胡亚辉,李向军,等.超声振动钻削皮质骨切屑形成机理及表面粗糙度研究[J].天
津理工大学学报,2019,35(6):9-12,40.
[6]戴晨伟,殷振,赵盟月,等.超声椭圆振动切削轨迹倾斜角度及速比对工件表面微观形貌的影
响[J].工具技术,2021,55(2):34-38.
[7]孟倩.圆片刀超声切削Nomex蜂窝芯表面质量研究[D].大连理工大学,2020.
作者简介史春光(1993-),男,安徽阜阳人,硕士研究生,研究方向:高效精密加工。E-mail:
1372223426@qq.com通信作者张敏良,男,教授级高级工程师。E-mail:jx9988@163.com
相关链接