1、 引言
镍基高温合金材料是一种沉淀强化型高温合金,具有强度、硬度以及高温力学性能优等特性,被广泛用于航天航空、国防、能源等重要领域[1,2] 。
GH4169镍基高温合金在 750℃~ 950℃下能稳定工作,被用作航空发动机涡轮叶片[3] 。GH4169 高温合金在高温下具有优异的抗氧化性、抗热腐蚀性能及较好的蠕变强度,导致在加工中硬化严重,在业内被称为典型的航空难加工材料。机加工过程中,镍基高温合金硬度高且加工硬化严重,刀具不仅要承受持续的磨粒磨损,还要承受持续的热和力冲击,导致刀具发生多种失效。其主要失效方式有前刀面磨损、沟槽磨损、积屑瘤、后刀面磨损以及崩刃等。
在切削高温合金时涂层可以起到隔绝热量与减磨耐磨的效果,与未涂层刀具相比,涂层刀具的寿命明显提升。较为常见的高温合金切削用涂层有 Al-CrN,TiAlN,TiSiN 和 TiAlSiN 等[4 -6] 。Bhatt A.等 [7]在车削 Inconel 718 合金时,对比了无涂层、单一涂层(TiAlN)和复合涂层(TiCN-Al203 -TiN) 3 种硬质合金刀具的切削效果,结果发现,在高速切削时复合涂层硬质合金刀具表现出最好的耐磨性。Fox-Rabi-novich G.S.等[8] 在硬质合金刀具表层涂覆纳米级AlTiN-Cu 材料,并使用该刀具切削 Inconel 718 合金,该涂层具有自润滑和改善散热的作用,能显著延长刀具寿命。Yi J. Y. 等[9] 研究 AlTiN,AlTiN-Ni1. 5和 AlTiN-Ni3等多层复合纳米涂层硬质合金刀具切削 Inconel 718 合金,刀具的主要失效形式为前刀面黏结,在相同的切削条件下,AlTiN-Ni1.5 刀具磨损量最小,其特殊的纳米晶结构和高韧性可使刀具寿命延长 2 倍。
为获得高切削寿命的高温合金刀具,本文通过不同涂层工艺,制备了三种 TiAlSiN-TiAlN 复合涂层刀具,研究了其对GH4169镍基高温合金切削性能的影响。对涂层的厚度生长形貌、切削过程中后刀面的磨损量、切削力和切削热等进行了分析,为高效切削GH4169镍基高温合金提供参考。
2、 实验过程与方法
2.1 涂层制备
本研究制备的 TiAlSiN-TiAlN 复合涂层,采用自主研发的多功能一体化涂层装备中的电弧离子镀功能制备。试样采用 TNMG160408 型号硬质合金刀具,涂层前对试样进行预处理,即先用酒精清洗抛光后的金属陶瓷试样表面污物,再将干净表面喷砂处理之后放入涂层沉积室中。在涂层室进行二次清洁:在真空度为 5.0 ×10-3 Pa 时,利用氩离子轰击试样表面并加热 60min。随后在约 450℃ 的氮气和氩气氛围中利用纯度为 99.99%、成分为 Ti50Al50 的溅射靶、Ti50Al40Si10 在金属陶瓷试样表面交替制备 TiAlN 和 TiAlSiN 涂层。涂层沉积过程中,弧靶电流为 120A,偏压分别为 -60V,-80V,-100V,沉积总时间为 60min,沉积完成后,试样在氩气保护气氛中冷却40min。为避免可能存在的偶然误差,试样位置随机摆放并在涂层过程中随摆架转动。
2.2 表征
采用 Hitachi 公司的 SU -3500 型扫描电子显微镜(SEM)进行观测,同时利用Oxford 的 IE2500 型能量色散光谱仪(EDS)分析元素组成、原子百分比及元素扩散等情况。采用 MFT - 4000 多功能表面性能测试仪划痕法测定涂层与基体的结合力,设置关键参数:最大载荷150N,滑动长度5mm,加载速度100N/min。采用 Bruker Hysitron TI Premier 纳米压痕仪分析涂层硬度及弹性模量,最大载荷 8000μN,压头选用 Berkovich 低载金刚石锥形头,每个涂层标块采集 8 ~10 个点,取平均值作为最终结果。
2.3 实验内容
2.3.1 切削有限元仿真
采用 AdvantEdge FEM 软件进行切削仿真,被加工材料选择GH4169高温合金,性能如表 1 所示。硬质合金及涂层性能采用参考文献[4]中相对应数值,工件采用最大网格尺寸为 2,最小网格尺寸为 0.15,网格等级 G = 0.5。切削参数为切削速度 V c =60m/min,切削深度 ap = 0.1mm,切削进给量为 0.2mm/r,其主要成分和物理性能如表 2所示。
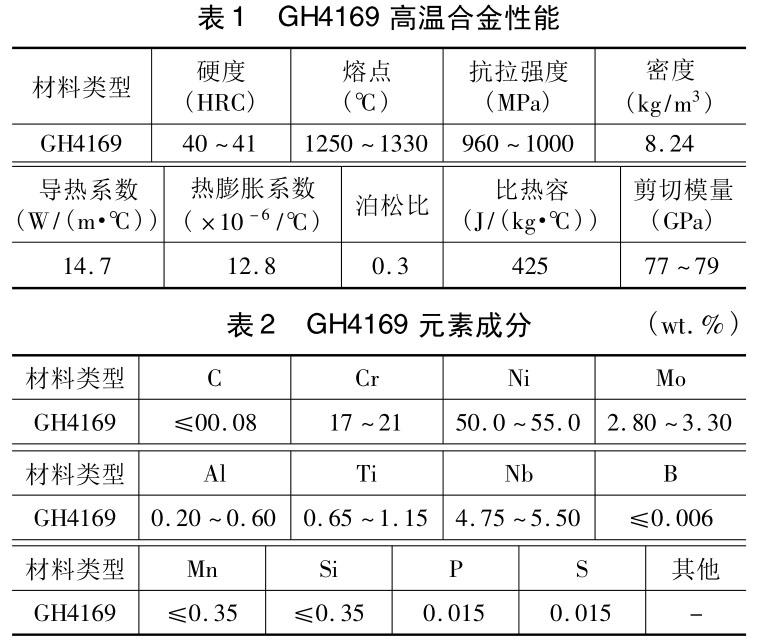
2.3.2 切削实验
使用显微镜对刀具进行检测,确认无缺陷后进行切削。刃口完整的刀片 ( 未涂层和涂层) 在CK6140 卧式数控车床上进行实验。其中切削参数为切削速度 V c =60m/min,切削深度 ap =0.1mm,切削进给量为 0.2mm/r,每 2min 通过 VMS - 4030 影像测量仪观测刀片刀尖的磨损形貌,进入到稳定磨损阶段后,通过 SEM 扫描电镜及 EDS 进行形貌和元素分析。
3、 结果与分析
3.1 涂层组织和性能
三种不同偏压下 TiAlN/TiAlSiN 复合涂层断口形貌如图 1 所示。可以看出,三种不同偏压下的涂层均由上下两层涂层组成,三种样品上的涂层厚度分别为 2.21μm,2.37μm,2.74μm,三组图中均没有出现明显的由于涂层沉积残余应力产生的裂纹。其中 -80V 和 -100V 制备的涂层均可发现底层 TiAlN材料呈现较为明显的柱状晶结构,且 -100V 偏压下制备的涂层较为平整且致密,- 60V 偏压下制备的双层涂层中底层 TiAlN 柱状晶生长状态不明显。
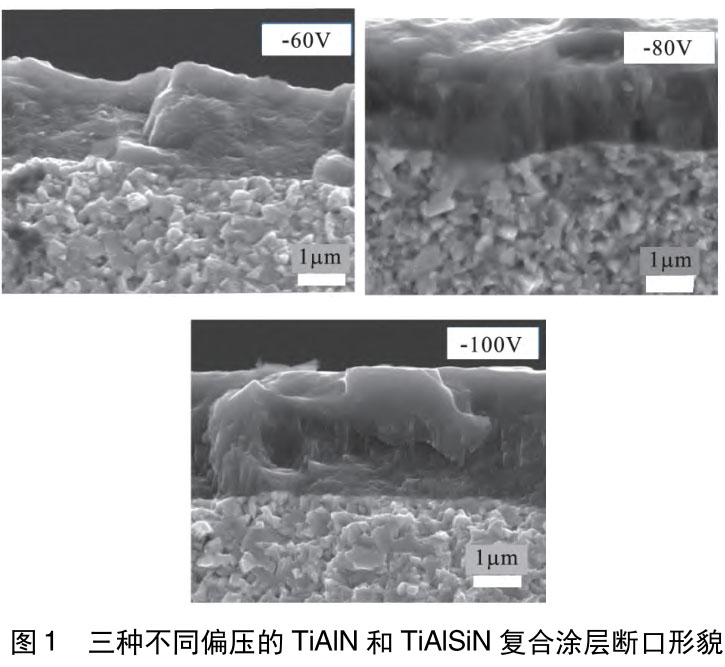
图 2 为涂层元素分布,表 3 为涂层元素成分,图3 为三种不同偏压下的 TiAlN/TiAlSiN 复合涂层表面形貌。
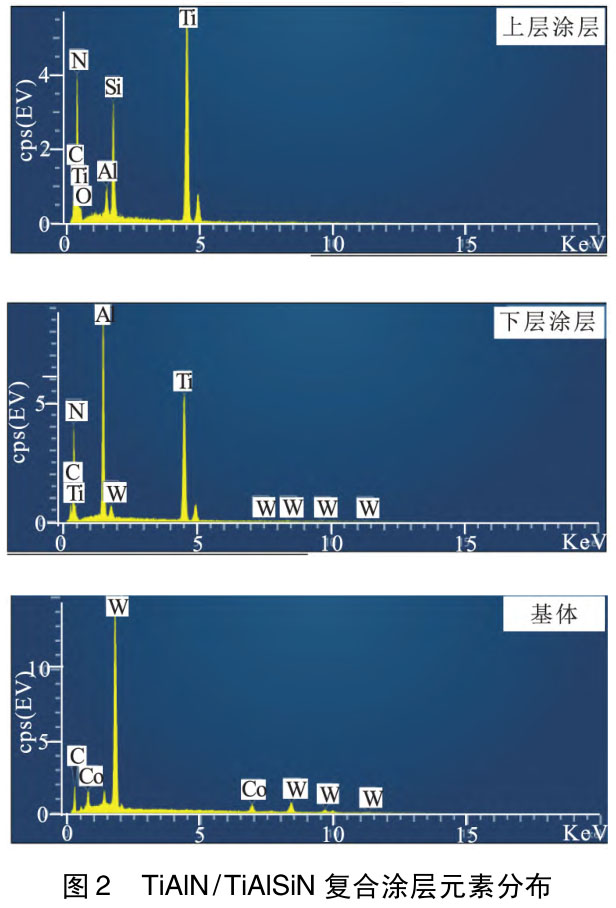
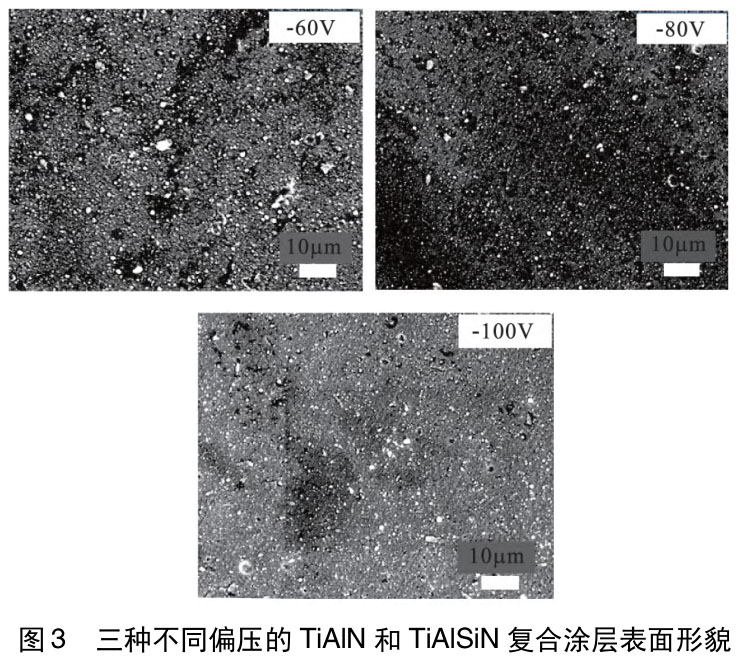
从图 3 中可以发现,三种涂层表面没有特别明显差异,三种表面均较为平整,没有发现明显的大颗粒。随着偏压的增加,大颗粒数量减小,表面的孔隙减少,涂层致密性提高。偏压增加使得等离子体的活化能增强,涂层沉积效率增加,并且涂层生长效率增加,涂层堆砌更为致密。偏压的增加还使得涂层择优生长趋势增强,因而 TiAlN 涂层随着偏压的增加,其柱状晶趋势更为明显。大偏压可以让荷能粒子的轰击能量增加,高的轰击能量使涂层的反溅射现象增强,涂层表面沉积的吸附力较低的大颗粒在反溅作用下被击碎或者溅射掉,因此涂层表面颗粒较为细小。但过高的偏压会使反溅射过大,涂层表面生长反而变差,从显微组织结果可以得知,-100V 偏压下,涂层的反溅射减小,负偏压也会使等离子体离子以更高的能量撞击基板表面,从而提高其温度并使薄膜表面平滑。
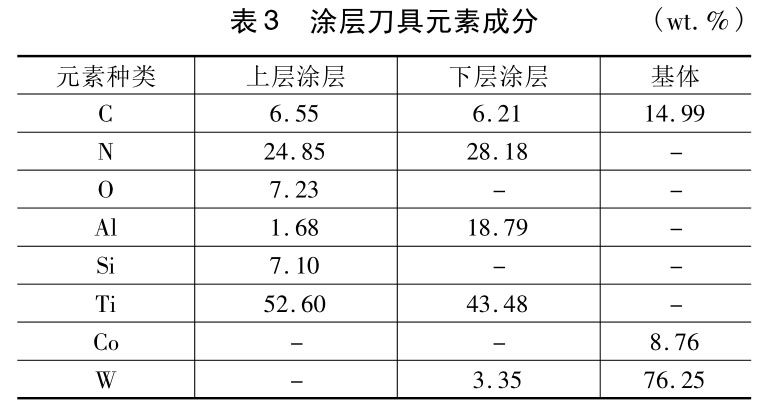
表 4 为不同偏压下 TiAlN/TiAlSiN 复合涂层的机械性能。
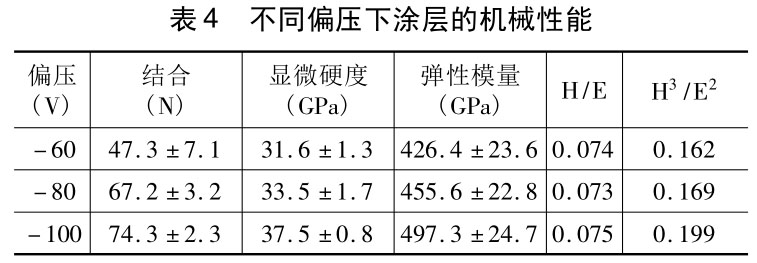
从表中可以发现,随着偏压的增加,复合涂层与基体结合力增加,并且在偏压为 - 100V 时,结合力获得最大值 74.3N。涂层的硬度和弹性模量也随着偏压的增加而增大,涂层机械性能的提高,均优于涂层生长。在偏压范围内,随着偏压的增加,涂层的致密性和择优取向性明显增强。H/E 表征涂层的抗弹性变形能力,其值越大则代表抗弹性变形能力越强,而 H 3 /E 2 表征涂层的抗塑性变形能力,其值越大,表征涂层的抗塑性变形能力越好。偏压的增加对涂层抗弹性变形能力影响不大,但抗塑性变形能力随着偏压的增加得到明显增强。
3.2 切削性能
为了对比三种偏压下涂层刀具的切削性能,以GH4169 高温合金为被加工材料,以切削速度 V c =60m/min,切削深度 a p = 0.1mm,切削进给量为0.2mm/r 进行了切削实验。根据 ISO—3685 标准,当后刀面磨损量大于 0.3mm 时,判定切削刀具达到其切削寿命。
图 4 为三种不同偏压下涂层刀具与未涂层刀具切削过程中,后刀面磨损量与时间的变化曲线。从图中可以看出,涂层刀具的切削磨损量明显小于未涂层刀具,且随着偏压的增加,涂层刀具的寿命得到提高,当 -100V 偏压时,切削寿命最高,约在 38min时,后刀面磨损量达到 0.3mm。
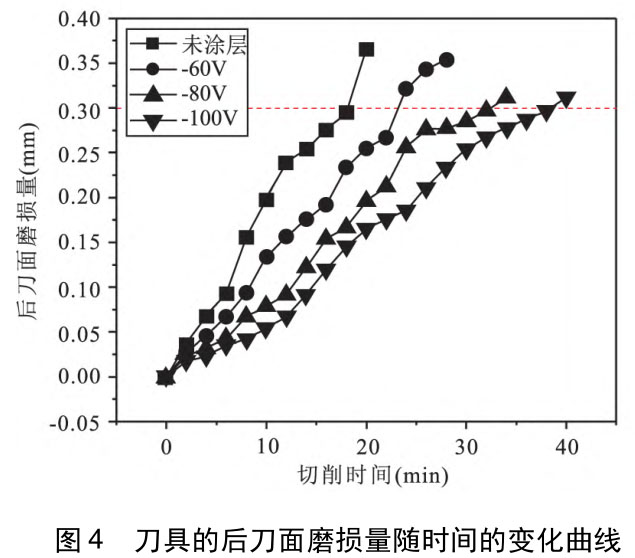
在切削过程中,由于涂层刀具的表面硬度明显提高,因而其刀具耐磨性会增强。为更清楚地了解切削过程的变化机理,对三种不同偏压下涂层刀具的切削过程进行了模拟仿真。如图 5 所示,三组涂层刀具切削过程均经历短暂的磨合后达到稳定。在稳定磨损期,切削力出现稳定性的波动。随着偏压增加,涂层刀具的切削力明显增加,且在 - 100V 偏压下制备的涂层刀具主切削力最大约为 1500N。图 6 为三种不同偏压下的 TiAlN/TiAlSiN 复合涂层刀具切削后的温度分布云图,刀尖和工件接触处的切削温度最高。这是由于在切削过程中,刀尖和被加工材料发生剧烈的弹塑性变形,当剪切力大于被加工材料的剪切极限时,被加工材料被剥离,产生切屑。随着偏压的增加,涂层刀具的最高切削温度也增加,且当偏压为 - 100V 时,切削温度达到最高值约 1200℃。由于在切削仿真过程中,仅考虑刀具和工件的受力、挤压、传热等理想条件,且刀具涂层、基体以及被加工材料均视为刚体,并未考虑涂层表面涂层颗粒的分布状态、孔隙、晶体状态以及切削过程中的扩散、氧化等化学或热力学过程,且TiAlN/TiAlSiN 涂层的热导率远小于含有金属相的硬质合金基体,因而随着偏压的增加,涂层厚度增加,使得切削力和切削热均增加。
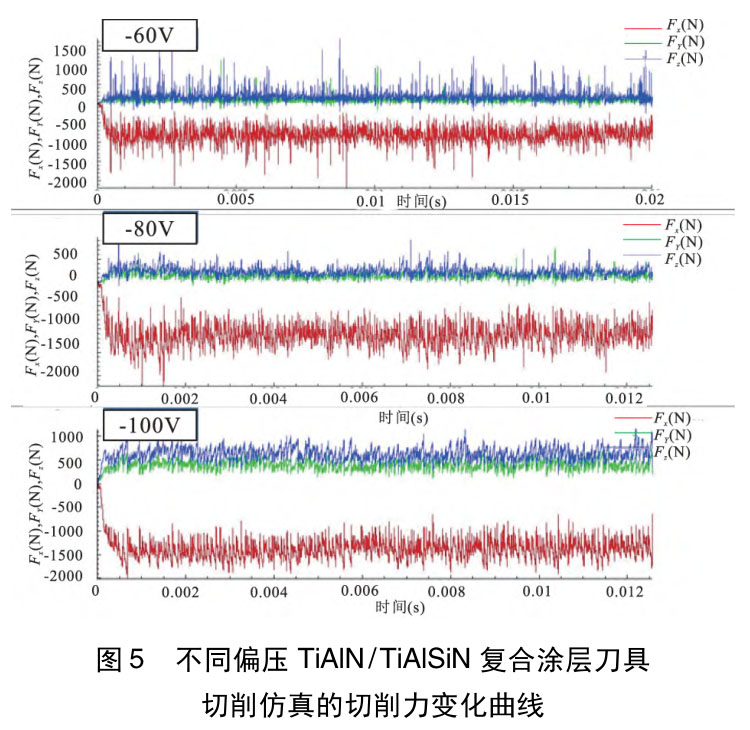
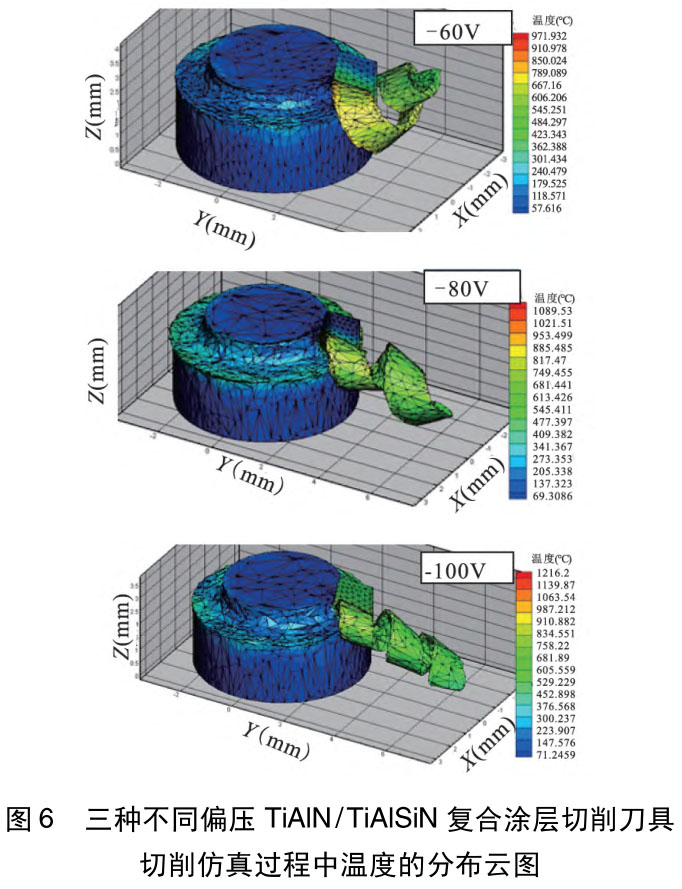
图 7 为未涂层刀具和不同偏压下 TiAlN/TiAl-SiN 复合涂层刀具切削高温合金时后刀面磨损的光镜和 SEM 形貌。
结合表 5 可以发现,对于未涂层刀具,表面磨损严重,主要是由于切削过程中磨粒磨损产生的沟槽,涂层刀具的后刀面沟槽较少,主要发生了扩散磨损和氧化磨损,并且随着偏压的增加,刀具的整体磨损量减小。对于未涂层刀具,在切削过程的交变应力作用下,剥离高温合金材料时,硬质合金刀具表面的硬质相颗粒脱落,后刀面的磨损过程由高温合金—硬质合金的双体摩擦变为高温合金—硬质颗粒—硬质合金的三体摩擦,因而在表面产生磨粒磨损。
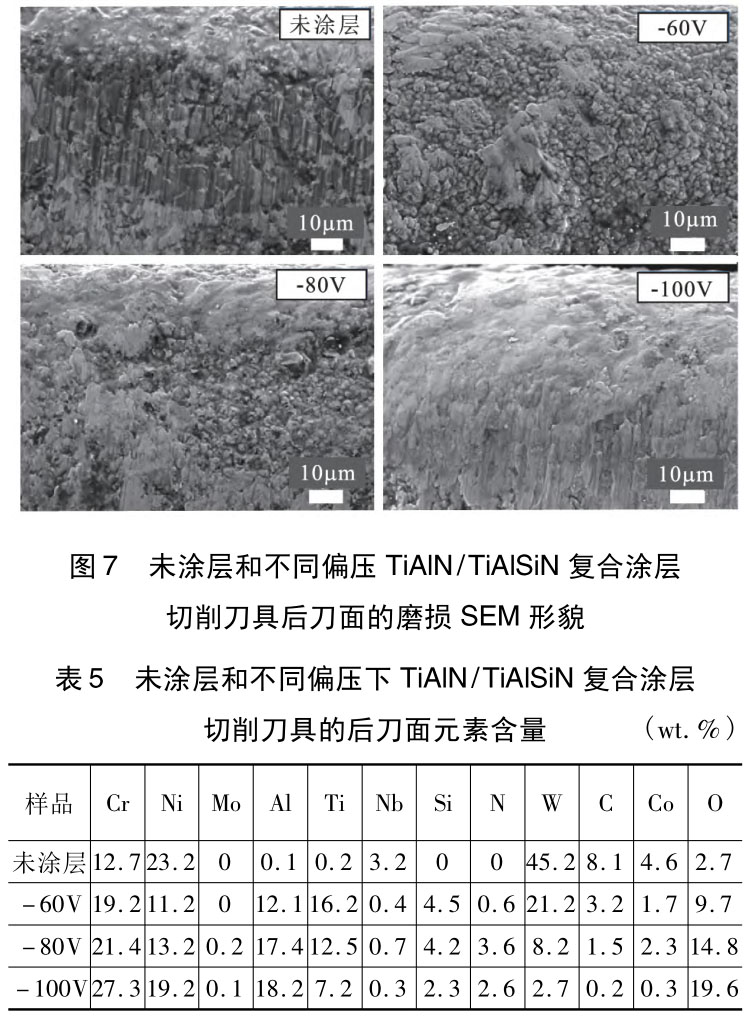
由于硬质合金表面的硬度相对于 TiAlN/TiAl-SiN 陶瓷涂层较小,表面磨损较为严重。在硬质合金刀具表面进行涂层后,磨粒磨损减小,由于涂层的热导率远小于含有金属黏结相的硬质合金,因而涂层刀具接触点挤压摩擦等交变应力产生的热量,比未涂层硬质合金更难散去,故涂层后刀具接触点的温度更高,并且随着偏压的增加,涂层厚度增加,涂层致密度增加,接触点的温度增加,被加工材料向刀具元素的扩散增强,表面氧化效应增强,因此随着涂层偏压的增加,后刀面的 Ni,Cr,O 等元素增加。由于 Ni,Cr,Al 等元素在氧化过程中容易在表面形成一层较为致密且具有一定润滑特性的氧化膜,润滑膜对表面产生保护作用,因此偏压 - 100V 时,TiAlN/TiAlSiN 复合涂层刀具切削寿命最长。
4 、结语
针对GH4169镍基高温合金的切削问题,通过制备 TiAlN/TiAlSiN 复合涂层刀具研究了不同偏压下 TiAlN/TiAlSiN 复合涂层刀具的涂层显微组织、力学性能以及切削GH4169镍基高温合金时的切削性能,结论如下。
(1) 三种不同偏压下的涂层厚度分别为2.21μm,2.37μm,2.74μm,其中 -80V 和 -100V 偏压下制备的涂层在底层 TiAlN 有较为明显的柱状晶结构,且-100V 偏压制备的涂层平整且致密,并且随着偏压的增加,大颗粒数量减小,表面的孔隙减少,涂层致密性得到提高。
(2)偏压的增加,复合涂层与基体结合力增加,并且在偏压为 - 100V 时,结合力获得最大值为74.3N。涂层的硬度和弹性模量也随着偏压的增加而增大,涂层机械性能提高,在偏压范围内,随着偏压的增加,涂层的致密性和择优取向性明显增强。
(3)切削GH4169高温合金时,涂层刀具的切削磨损量明显小于未涂层刀具,且随着偏压的增加,涂层刀具的寿命提高,当 - 100V 偏压时,切削寿命最高。切削过程中,Ni,Cr,Al 等元素在氧化过程中容易在表面形成一层较为致密且具有一定润滑特性的氧化膜,氧化膜的形成对刀具有一定的保护作用,因此偏压 - 100V 时,TiAlN/TiAlSiN 复合涂层切削刀具切削寿命最长。
参考文献
[1]杜金辉,赵光普,邓群,等.中国变形高温合金研制进展[J].航空材料学报,2016,36(3):27 -39.
[2]师昌绪,仲增墉.我国高温合金的发展与创新[J].金属学报,2010,46(11):1281 -1288.
[3]李卿,郭鸿镇,王彦伟,等.GH4049 合金的热变形行为及组织演变[J].材料工程,2014(12):55 -59.
[4]李锋,刘维伟,余斌高,等.TiAlN 涂层刀具高速铣削GH4169 刀具磨损形貌及机理分析[J].航空精密制造技术,2016,52(1):34 -38.
[4]季思源,万维财,彭卓豪,等.切削高温合金用涂层的研究进展[J].工具技术,2022,56(2):3 -10.
[6]Shokrani A,Betts J,Jawahir I S.Improved performance and surface integrity in finish machining of Inconel 718 with e-lectrically charged tungsten disulphide MQL[J].CIRP An-nals,2022,71(1):109 -112.
[7]Bhatt A,Attia H,Vargas R,et al.Wear mechanisms of WC coated and uncoated tools in finish turning of Inconel 718[J].Tribology International,2010,43(5):1113 -1121.
[8]Fox-Rabinovich G S,Yamamoto K,Aguirre M H,et al.Multi-functional nano-multilayered AlTiN/Cu PVD coating for machining of Inconel 718 superalloy[J].Surface and Coatings Technology,2010,204(15):2465 -2471.
[9]Yi J Y,Song Y C,Xu Y C,et al.Effects of Ni content on mi-crostructure,mechanical properties and Inconel 718 cutting performance of AlTiN-Ni nanocomposite coatings[J].Ce-ramics International,2019,45:474 -480.
第一作者:徐兴伟,高级工程师,中国航发成都发动机有限公司,610503 成都市
First Author:Xu Xingwei,Senior Engineer,AECC Chengdu Engine Co.,Ltd.,Chengdu 610503,China
通信作者:熊计,教授,四川大学机械工程学院,610065 成都市
Corresponding Author: Xiong Ji,Professor,School of Me-chanical Engineering,Sichuan University,Chengdu 610065,China
通信作者:刘俊波,副研究员,四川大学机械工程学院,610065 成都市
Corresponding Author: Liu Junbo,Associate Researcher,School of Mechanical Engineering,Sichuan University,Chengdu 610065,China
相关链接